What is 5 axis machining services? Working principle, types and benefits
The concept of machining has changed over the past few years. The world has moved on from simple machining processes and tools to more advanced and complex processes and tools. One of the most advanced machining processes today is 5 axis machining.
However, sometimes when it comes to specific 5 axis CNC machining, most people’s first impression is: high-tech, expensive, and difficult to operate, but is 5 axis machining really like this?
Read on as we provide the answer to this question and other important information about this machining.
1.What is 5 axis machining?
This machining relies on the tool moving in five different directions, and the tool rotates around these directions. It is a multi-axis subtractive manufacturing process in which the machine shapes the workpiece material and moves in 5 directions or perpendicular directions.
The directions of movement include: X, Y, and Z, as well as A and B. 5 axis machining allows the operator to machine the part from all directions and axes in a single operation.
Therefore, there is no need to manually reposition the workpiece between operations. In addition, it saves time and is ideal for manufacturing highly complex parts that require precision.
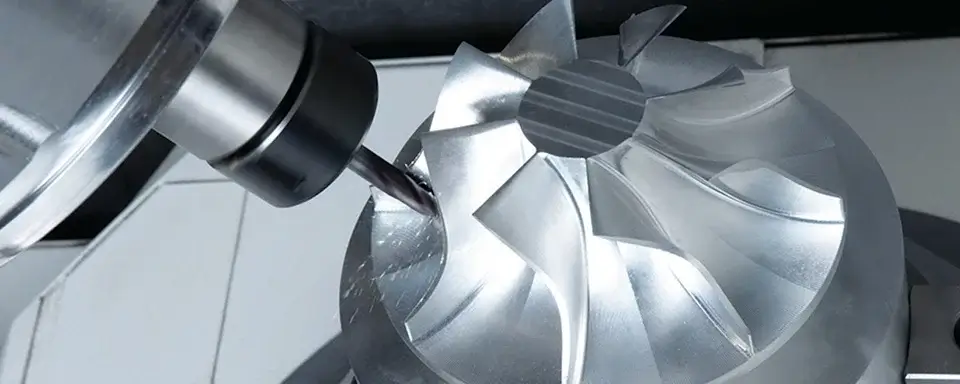
2.What does the “5” in 5 axis stand for?
The 5 in 5 axis refers to the fact that in addition to the traditional three axes of X, Y, and Z, 5 axis machining machines have two additional axes, for a total of 5 axes, of which the 4th axis is the A axis, which rotates around the X axis, and the 5th axis is the B axis, which rotates around the Y axis.
This additional axis enhances the type of work that the machine can perform and the level of detail that can be cut.
3.Why use CNC for 5 axis machining?
This involves 5 axis machining on a CNC machine. 5 axis CNC machines offer three linear axes and two rotary axes that work together to produce highly complex parts.
Adding the 5th axis to this machine allows engineers and machinists to machine up to 5 sides of a workpiece in a single operation.
5 axis CNC machining is beneficial to manufacturers because it can save manufacturing time and costs while ensuring that products get to market faster.
Also note that the type and configuration of a CNC machine determines its general speed and direction.
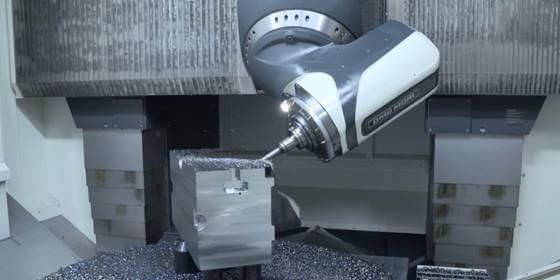
4.How do 5 axis CNC machines work?
5 axis CNC machines operate automatically with little to no human intervention. It uses a rotating cutting tool to shape the material placed on the platen of the machine.
However, placing the material on the platen is the final stage of the 5 axis CNC machining process. The first step in 5-axis CNC machining is to make a CAD design of the part and convert it into CAM. CAM or Computer Aided Manufacturing is a software that helps to generate CNC alphanumeric language or G-code.
The next stage in the process is to upload the G-code to the 5 axis CNC machine. The G-code is very important as it contains instructions that tell the machine to execute the tool path and select the right tool for machining.
5.Types of 5 axis CNC Machines
There are operations where a 5 axis CNC machine can save you a lot of time and enhance your current processes. There are various types of these machines to meet the needs of the growing manufacturing industry. The unique thing about 5 axis CNC machines is the arrangement of the rotary axes.
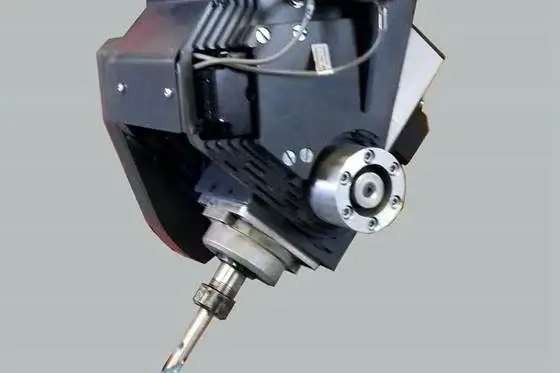
1) Head/Head
In this type of CNC machine, the rotary axes are housed inside the spindle head. In this part, you do not need to worry about tool interference with the machine spindle head as the 5-axis apex is located on a specific platform.
Another reason not to worry about interference is that this 5 axis vertex moves through a fixed table, ensuring that the workpiece remains in place.
This 5 axis machine design allows the vertex to move around a specific part during machining. Therefore, Head/Head CNC machines are ideal for producing large parts. However, along the rotary axis, this design has limited movement.
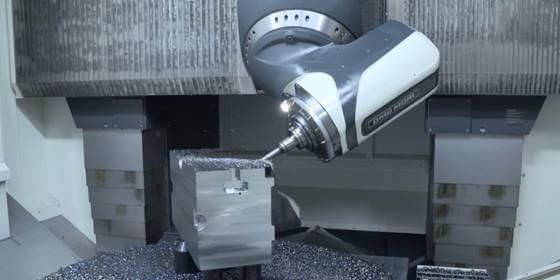
2) Table/Head
This setup also has two rotary axes, one in the head and the other on the rotary table. The rotary axis is located in the head and has a limited range due to the location of this axis. On the other hand, the range of a rotary axis placed on the table is unlimited.
One advantage of this setup over Head/Head is that there is no need to worry about reaching a specific limit because the part is always rotating. Conversely, because the part or workpiece is located on the rotary axis, the design of the CNC machine limits the number of parts it can produce.
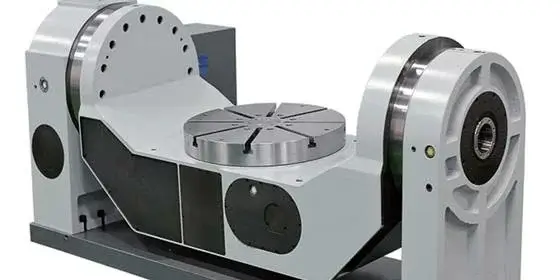
3) Table/Table
This setup has both rotary axes mounted on the table. The range of the rotary axis is severely limited, but the range of the rotary axis is unlimited. This makes this type of machine ideal for machining undercuts.
In addition, the table/table has the smallest working range compared to other machine arrangements. It is also slower than other machines because it does not have the specialized motors that make other machines run fast.
It is also not very suitable for machining large or heavy parts because they cannot carry much weight.
6.Advantages of 5 axis CNC machining services
This machining method has many advantages for many industries because it can machine 5 different sides of a workpiece at the same time. These advantages include cost-effectiveness and efficient machining. Here are the main advantages of 5 axis CNC machining.
1) Machining complex shapes
The additional axes added to this machine make it easy to machine complex designs and geometries. In addition, machining difficult angles and arcs (which previously required the use of multiple special fixtures) is now feasible with 5 axis CNC machines.
In addition, the machine is able to rotate the part during a single operation, so the required geometry can be achieved without complex machines or fixtures.
2) High precision and high repeatability
Manual machining operations require additional setups to achieve the best machining results. But these additional setups often introduce design variations and errors, causing machinists to lose alignment during the machining process.
However, 5 axis CNC milling involves minimal setup, eliminating the possibility of errors while improving accuracy.
In addition, most 5 axis CNC machines used by machinists today eliminate the need to manually reposition the workpiece during machining. This ensures improved machining tolerances.
In addition, using shorter cutting tools in certain machine configurations can extend tool life while ensuring repeatability.
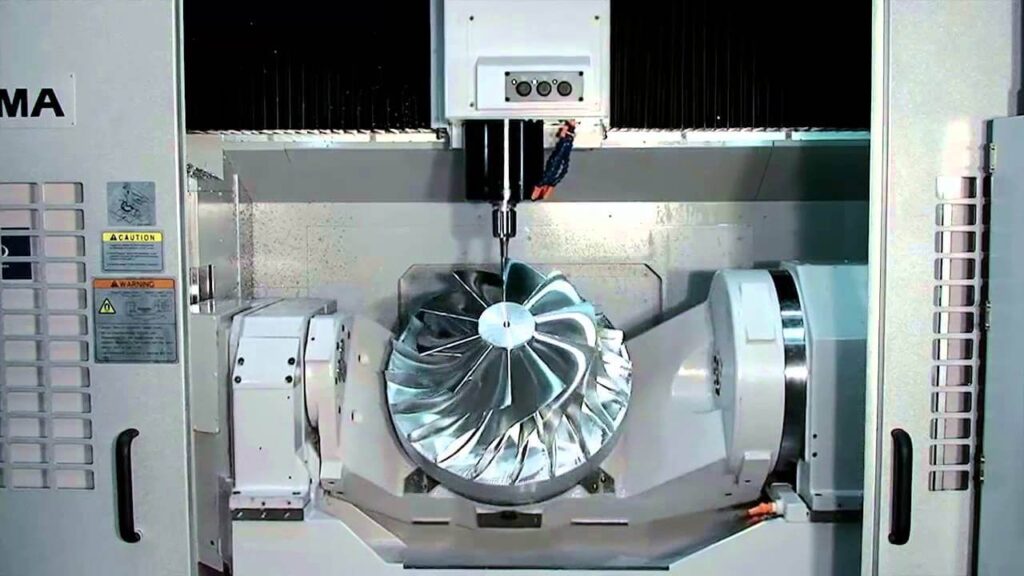
3) Efficient Setup Operations
The process of setting up a 5 axis CNC machine is relatively easier than setting up a 3-axis machine. The reason is that a 5 axis CNC machine allows working on five surfaces simultaneously.
In addition, 5 axis machines are capable of machining contoured parts with a single structure. However, with a conventional 3-axis machine, multiple setups are required to work on multiple surfaces.
4) High-quality Surface Finish
Due to the additional axes, 5 axis CNC machines have a smoother surface finish. These additional axes bring the workpiece closer to the cutting tool, making it easier to achieve the desired shape.
At the same time, it also allows machining with shorter cutting tools.
When using shorter cutting tools, there is almost no vibration, which reduces the chance of leaving marks on the finished surface. In addition, when using vertical processing technology, the spindle utilization rate of processing inclined surfaces will also be improved.
5) High production efficiency
Five axis machining can effectively reduce part processing time and auxiliary time, and the large spindle speed and feed range enable the machine tool to exert powerful large cutting capabilities.
Five axis CNC is entering the era of high-speed machining. The rapid movement positioning and high-speed cutting of five-axis machining shorten the turnover time of semi-finished products.
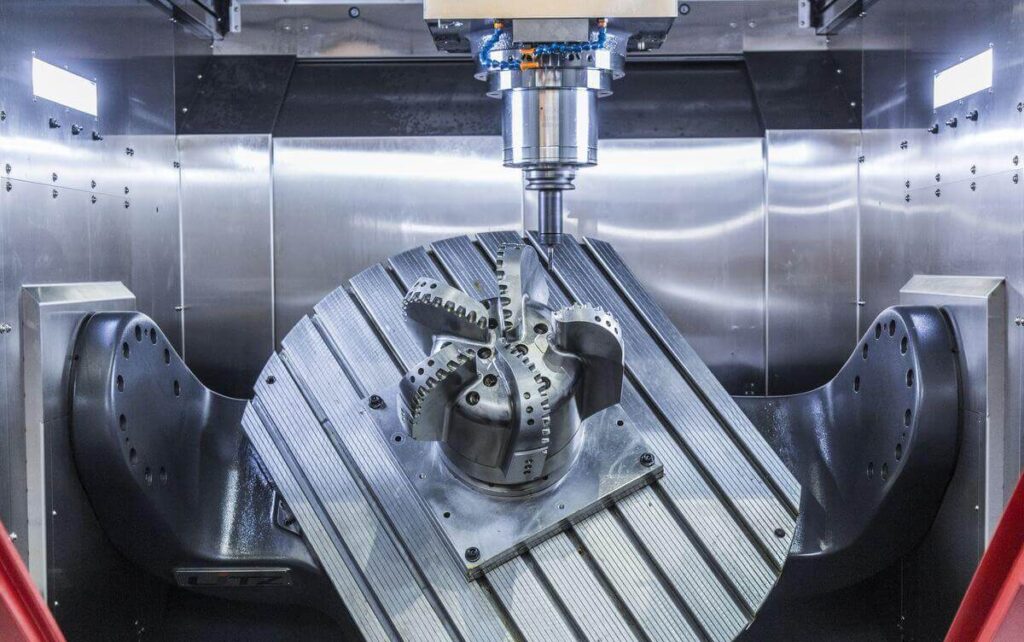
7.Disadvantages of 5 axis CNC machining services
5-axis has many advantages and importance in part manufacturing. However, 5 axis machining is not all plain sailing and there are some disadvantages. The following are the disadvantages of 5-axis machining:
1) High cost
The cost of purchasing a 5 axis CNC machine is much higher than the cost of purchasing a 3-axis machine. The same is true for the software required to operate the machine.
In addition, it is more difficult to maintain a 5 axis CNC machine than a CNC machine. Therefore, cost is one of the main disadvantages of using a 5 axis CNC machine for machining.
2) Programming complexity
The programming required for a 3-axis machine is different from that for a 5 axis machine. This is mainly because of the addition of two rotational motions, which makes the resulting synthetic motion trajectory complex.
For example, when programming 5 axes, each axis’s individual motion must be considered to avoid collisions and interference. In addition, achieving better surface quality and accuracy requires more complex programming.
3) Requires higher operating skills
5 axis CNC machining involves the use of advanced technology. Therefore, a skilled operator is required to make full use of the machine. However, hiring a skilled operator also increases labor costs.
8.What types of parts can be machined using a 5-axis machining center?
5 axis CNC machining can produce a variety of parts. These parts often have complex geometries and intricate shapes. Here are some of the parts that can be machined using 5-axis machining.
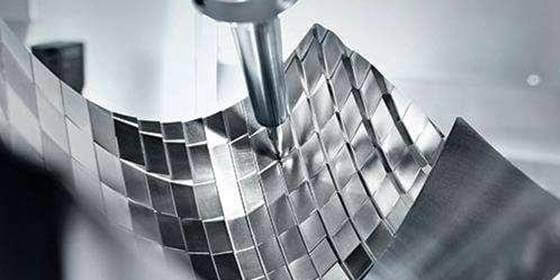
1) Complex curved parts
Complex curved parts are parts that are often encountered in different fields such as aviation, aerospace, and electronics. It is difficult to achieve such complex surfaces using ordinary CNC machines.
Common complex surfaces that 5 axis machining can help produce include spheres, turbine engine blades, marine propellers, impellers, etc.
2) Optical disc parts
5 axis CNC machining is also very suitable for machining drone parts. It is suitable for machining plates and plates, especially those with end-face distribution holes or radial holes.
It is also suitable for manufacturing machine motor covers. It should be noted that applying 5 axis CNC machining to such parts requires the use of a horizontal machining center or a vertical machining center. The selected machining center depends on the specific hole direction.
3) Box-shaped parts
It is relatively difficult to process box-shaped parts using ordinary machining tools because multiple clamping and alignment are required. Five-axis machines can process multiple surfaces at the same time, so it is easier to produce box-shaped parts with higher precision.
4) Special-shaped parts
Special-shaped parts refer to parts with irregular shapes, such as workpieces with mixed points, surfaces, and lines. It is very difficult or almost impossible to process such parts with traditional machining methods because the clamping pressure is difficult to control during machining.
However, with 5 axis machining, it becomes easier to complete machining using multiple workstations.
9.Difference between 5 axis and 3+2-axis machining
Most people don’t know that there is a difference between 5-axis machining and 3+2-axis machining, or even between 3-axis, 4-axis, and 5 axis CNC. In 5-axis machining, the rotation of the cutting tool is performed continuously along 5 axes.
On the other hand, in 3+2-axis machining, the machine tool executes a 3-axis program and the tool is locked at a certain angle. In addition, the locking angle depends on the two rotating axes.
Speed ​​is the main advantage of 5 axis machining over 3+2-axis CNC machining. The speed difference is because 3+2-axis machining requires constant stopping and starting of the machine to achieve the best tool orientation. Whereas with 5-axis CNC machining, there is no need to stop because machining involves a single operation.
10.Strategies to Get the Most Out of 5 axis CNC
Since most operators do not understand the full capabilities of 5 axis CNC machines. Therefore, here are some strategies that can help you get the most out of your 5 axis CNC machine.
1) Choose the Right Software and Controls
Before using a 5 axis CNC mill, you must get the right information. Getting the right information includes analyzing the accuracy and correctness of the design data. It is also important to validate the design process before converting the CAD design to a CAM equivalent.
With the right information, choosing the ideal CAD/CAM software and controls can accomplish the design task. This software is a simulation software used to monitor part dimensions, interferences, and tool lengths.
In addition, with this information, a cost analysis can be performed to ensure that the right and most cost-effective process is being adopted to complete the job.
2) Choose a Tool Detection System
Using the wrong tool increases the risk of error. Additionally, the wrong tool can easily wear out or break during machining, increasing production costs and reducing product quality.
One way to mitigate this is to use a tool detection system. This system helps you analyze the tool you are going to use, ensuring it is the right tool for the job and minimizing errors.
3) Prevent Collisions
Collisions can cause defects in parts or damage to machines. Fortunately, there are software tools that can help reduce this risk. So, how does it work?
The software simulates the design process and often finds collisions before they occur, providing a way to change the design commands. There are many such software, but popular ones include Predator and ModuleWorks.
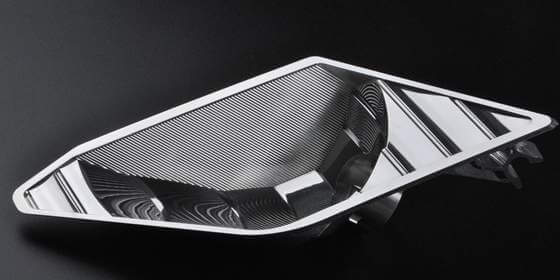
11.Industries that benefit from 5 axis CNC
5 axis CNC machining services offer a number of benefits to the industry, including reduced human error, improved product quality, and consistency. Many industries use this type of machining to manufacture products and parts, but the main ones include:
1) Medical Industry
Precision and accuracy are very important to this industry because part failure can cause disaster during surgery or testing or diagnosis of medical conditions.
5 axis CNC machining services can be applied in the medical industry for the production of research equipment, MRI machines, surgical implants, medical instruments, and orthopedic devices.
2) Electronics
Electronic devices are an integral part of our daily lives as they are part of commercial and consumer products.
5 axis CNC machining services help produce even the smallest components required for these electronic devices to function properly. It can be used to produce electronic housings, semiconductors, hardware, metal laths, heat sinks, and printed circuit boards.
3) Energy Industry
Parts in the energy industry must meet precise standards and specifications in order to prevent catastrophic failures. Moreover, when the parts used in this industry are not suitable, it often leads to the entire system going down, resulting in loss of revenue for the company involved.
5-axis machining services are employed in this industry to produce drills, pistons, rods, cylinders, and valves.
4) Aerospace Industry
This industry requires parts with complex shapes and contoured edges. Moreover, due to the use of parts with complex geometries, 5 axis machining services become the preferred process for machinists in this industry.
Moreover, the use of 5 axis machining services helps produce high-quality parts that meet industry standards.
12.Conclusion
5 axis CNC machining services help produce complex parts with high-quality surface finish. Although the initial cost is higher, this machining helps save money and time in the long run.
Due to its high part accuracy, this machining process can be applied in a wide range of industries such as aerospace, electronics, and medical.