The basics of boss machining
The term “boss machining” may not be well known in the world of precision engineering, but there is no doubt that it is a key element that underpins countless industries.Machining boss is also becoming an indispensable component.
Whether you are a novice looking to expand your knowledge or a seasoned professional seeking a deeper understanding, this article will serve as your comprehensive guide to what boss machining is, how it works, and why it is important.
1.Basic Definition of Boss Machining
In simple terms, a boss machining is a raised or thickened area on a workpiece, usually created through machining processes such as milling, turning, or drilling. These bosses play a key role in various engineering and manufacturing applications. They are an integral part of complex machinery, and their presence is often a testament to precision engineering.
The main purpose of boss machining is to provide a stable and specified location for various components such as threaded fasteners, mounting points, and even fluid passages. Let’s take a deeper look at its functions.
2.How Boss Machining Works
Boss machining is like a building block in the field of mechanical design and engineering. They have several key functions:
- Threaded connections: One of the most common uses of boss machining is to provide a secure connection point for threaded fasteners such as bolts, screws, or nuts. These bosses ensure that mechanical components are securely in place.
- Mounting Points: Boss machining serves as a reliable mounting point for other components. Whether it is a bracket, sensor or electrical connector, these bosses provide stability and precision.
- Reinforcement: Enhances the structural integrity of a part, making it more rigid and able to withstand mechanical stress.
- Fluid Passages: In some applications, machined bosses contain fluid or air passages, allowing for the integration of hydraulic or pneumatic components.
We will take a closer look at the manufacturing process and types of boss machining in the next section as we continue to explore the world of boss machining.
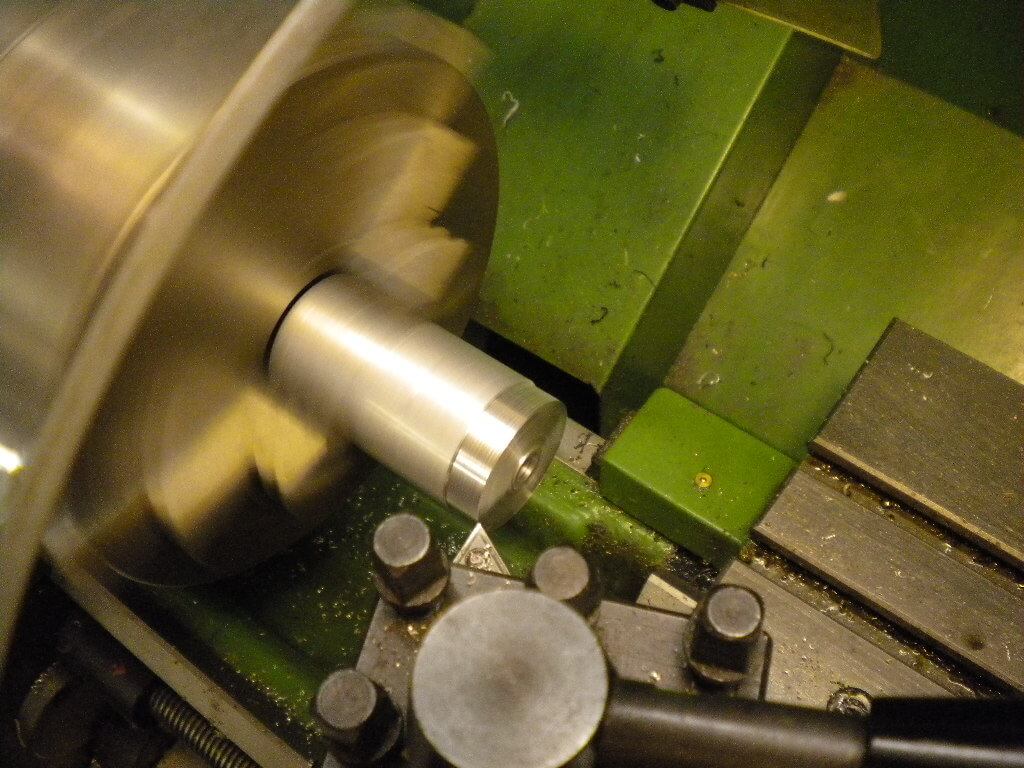
3.CNC Machining Processes and Machined Bosses
CNC (Computer Numerical Control) machining is at the forefront of machining technology. It is no surprise that CNC machining is often used in the production of machined bosses. The precision and versatility of CNC machines make them ideal for manufacturing these critical components.
CNC machines use computer-aided design (CAD) models to create machined bosses with extremely high precision. The process begins by feeding the CAD model into the CNC machine’s software. The machine then follows these precise instructions to remove material from the workpiece, shaping it into the desired machined boss.
This level of precision allows for the creation of complex, custom machined bosses to meet the unique specifications of a variety of applications. CNC machining is particularly beneficial for creating threaded bosses, as precise threads are essential for a secure fastener connection.
At Xavier, we take pride in our CNC machining capabilities, which include state-of-the-art milling services.
Our CNC milling services utilize advanced machinery and skilled machinists to create bosses that meet the highest standards of quality and precision. Whether you require an intricate shape or complex design, our milling services can accommodate a variety of boss types.
4.Manufacturing Process at boss machining
The manufacturing process for machined bosses involves several meticulous steps, each of which plays a critical role in ensuring the quality and functionality of the final product.
Step 1: Design
The design phase lays the foundation for the boss process. During this phase, engineers specify the size, features, and location of the boss within the overall design of the part or assembly.
The design of a boss process takes into account many factors, such as the type of fastener it will be used for, the workpiece material, and the expected mechanical loads. These considerations are critical to creating a boss that can withstand the stresses encountered in the intended application.
Step 2: Material Selection
Choosing the right material is a critical decision in the manufacturing process. The material chosen for boss machining can significantly affect its performance and durability. Common materials for boss machining include:
- Steel: Steel is known for its strength and durability, making it a popular choice for boss machining in heavy machinery and automotive applications.
- Aluminum: Aluminum is lightweight and corrosion-resistant, making it suitable for applications where weight reduction is required.
- Plastic: Certain applications benefit from boss machining made from high-strength plastics, which offer a balance between durability and weight.
Material selection depends on the specific application, and it is important to consider factors such as mechanical stress, environmental conditions, and cost-effectiveness.
Xavier is a trusted CNC machining service provider that offers a wide range of material options to meet your specific boss requirements. Our team of experts can guide you in selecting the ideal material for your application.
Step 3: Machining
The actual machining process involves removing material from the workpiece to form the machined boss. Machining processes may include:
- Milling: A rotating cutting tool removes material to form the boss shape. This is a versatile process that can be applied to a variety of boss types. Xavier’s state-of-the-art CNC milling services ensure precision and quality in every boss we produce.
- Turning: This process is used to create high-precision cylindrical bosses. It is commonly used for threaded bosses. Xavier’s CNC turning services are able to create complex cylindrical bosses to meet your exact specifications.
The choice of machining process depends on the design and requirements of the boss, as well as the capabilities of the machining equipment.
Step 4: Quality Control
Strict quality control measures are essential to ensure that the machined boss meets precise specifications. This step typically involves inspection, measurement, and testing to verify the size, surface finish, and function of the boss.
Quality control is especially important for threaded bosses, as accurate threads are essential for proper engagement of the fastener. Any deviation from the specified tolerance can cause problems during assembly or operation.
By following these steps during the manufacturing process, engineers and machinists can ensure that the machined boss meets the highest quality standards and performs as expected. The final component is critical to the functionality and reliability of a variety of mechanical systems and equipment.
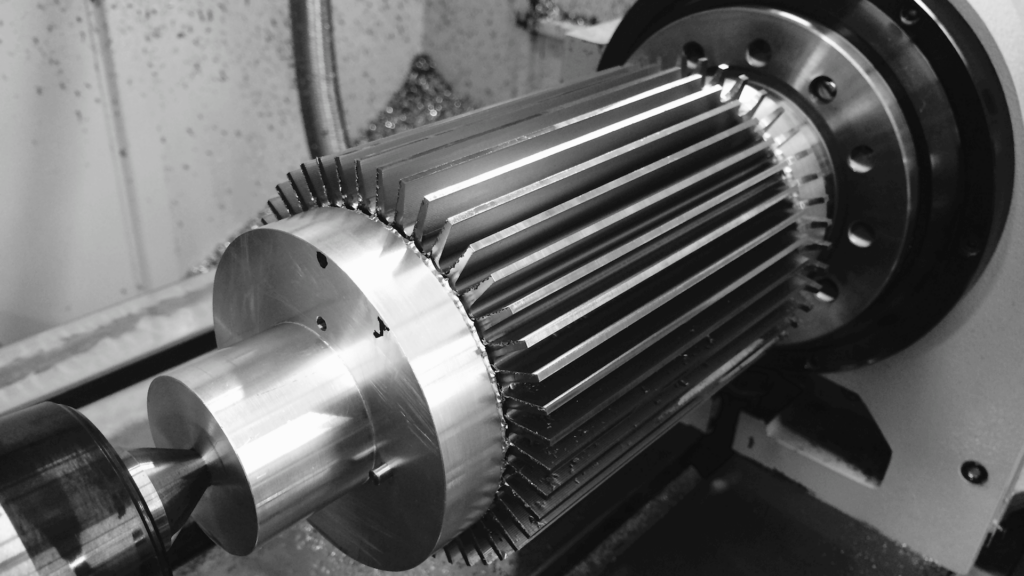
5.Different Types of Boss Machining
There are several types of boss machining, each tailored for a specific application:
1) Threaded Boss
Threaded bosses are designed to accommodate threaded fasteners, providing a secure connection. These bosses play a vital role in a variety of applications where a component needs to be securely fixed.
2) Blind Boss
Blind bosses are used when the connection point should not extend into the workpiece. Blind bosses are particularly useful when a clean, unobstructed surface is required.
3) Through Boss
Through bosses extend completely through the workpiece, providing multiple connection points. They are versatile and can be applied across a variety of industries. Xavier’s CNC machining services are able to produce through bosses to your exact specifications and quality requirements.
4) Flush Boss
Flush bosses are nearly flush with the surface, giving a seamless appearance. These bosses are often used in applications where aesthetics and a smooth finish are desired. Xavier’s expertise in precision machining ensures that the flush bosses meet not only functional standards, but also aesthetic standards.
The choice of boss type depends on the specific requirements of your project. Whether you need a threaded boss, blind boss, through-hole boss, or flat boss, Xavier’s machining services can provide you with a precisely customized solution.
6.Material Selection and Machined Bosses
Material selection for boss machining is a critical decision that significantly affects its performance, durability, and suitability for a particular application. Each material has unique properties that make it suitable for a specific use.
Here are some common materials used for boss machining:
1) Steel
Steel is known for its strength and durability. It is often the material of choice for boss machining in applications where sturdiness and load-bearing capacity are critical. Steel machined bosses are often used in heavy machinery, construction equipment, and automotive parts. Xavier offers steel machining services that ensure precision and quality for demanding applications.
2) Aluminum
Aluminum is a lightweight and corrosion-resistant material that is ideal for applications where weight reduction is a consideration. Aluminum machined bosses are frequently used in aerospace components, consumer electronics, and automotive parts. Xavier’s expertise in aluminum machining ensures that these bosses meet both structural and weight reduction requirements.
3) Plastics
High-strength plastics are popular for a variety of applications due to their balance between durability and weight. They can be used in consumer goods, medical devices, and automotive parts. Xavier’s precision machining services extend to using high-strength plastics to create boss machining that meets specific requirements.
4) Specialty Materials
In some cases, it may be necessary to use special materials, such as special alloys or composites. These materials are selected based on their unique properties, including resistance to extreme temperatures, corrosion environments, or specific electrical and thermal properties. Xavier’s machining capabilities can accommodate a variety of special materials, ensuring that the machined boss meets excellent standards.
The choice of material should be consistent with the boss’s intended function, mechanical stresses, environmental conditions, and cost considerations. As an experienced CNC machining service provider, Xavier provides comprehensive material selection guidance to ensure that your machined boss can meet your specific application needs.
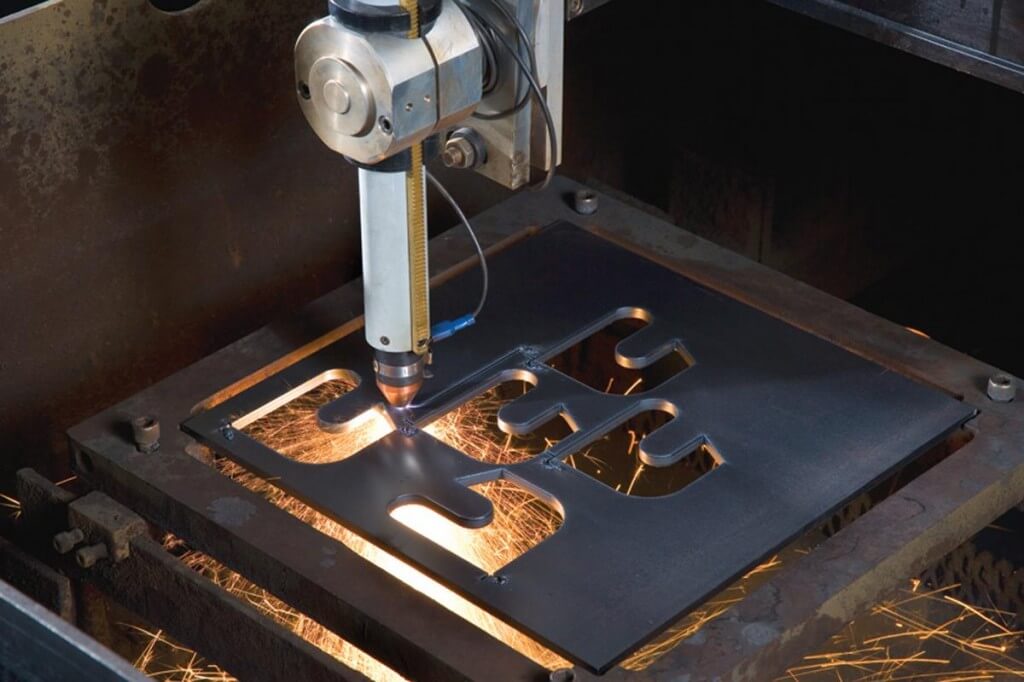
7.Real-world applications
Boss machining is essential to the function and reliability of various mechanical systems and equipment. Let’s explore some real-world applications to highlight their importance in different industries:
1) Automotive Industry
In the automotive field, boss machining is widely used in the assembly of engine, transmission, and suspension components. Threaded bosses secure critical engine components, ensuring their stability and reliability. Bosses are also used to mount sensors and connectors that are critical to vehicle control and safety systems.
2) Aerospace Industry
The aerospace industry relies on boss machining to ensure the structural integrity and safety of critical aircraft components. Threaded bosses are used to secure components in aircraft engines, while blind bosses are used to maintain the aerodynamic integrity of aircraft surfaces. The precision and quality of boss machining are critical in this high-risk industry.
3) Production Equipment
Boss machining is common in the assembly of complex machinery and production lines. Through-bosses are often used to provide multiple connection points for various components, enhancing the flexibility and functionality of the equipment. The reliability of boss machining is essential to maintaining the efficiency of the manufacturing process.
4) Robotics and Industrial Systems
In the field of robotics and industrial automation, precision is critical. Machined bosses are used to secure components, allowing robotic arms to perform complex tasks. The precise positioning and stability provided by machined bosses are essential to achieve the desired level of automation.
5) Consumer Products
Boss machining is used in numerous consumer products, from handheld electronic devices to kitchen appliances. Flush bosses are often used to ensure a smooth and beautiful surface, ideal for products where appearance is a priority. Reliable machining is essential to meeting consumer expectations for quality.
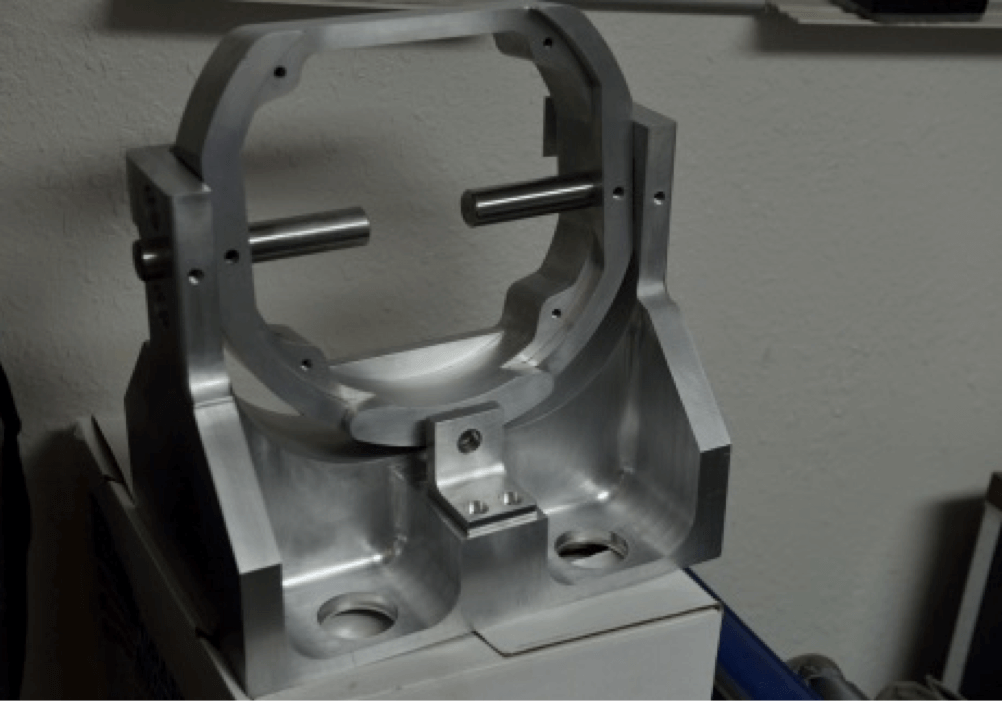
8.The Role of a CNC Machining Service Provider
As a professional manufacturing company, Xavier understands the complexity of manufacturing precision components such as boss machining. Our expertise in CNC machining enables us to provide high-quality boss machining that meets your specific requirements.
Here is how we can help you:
- Advanced Technology: Xavier uses state-of-the-art CNC machines capable of producing precision and intricate boss machining. Our technology ensures accuracy and consistency in every part we produce.
- Material Guidance: We provide expert advice on material selection to help you choose the most appropriate material for boss machining based on your application requirements.
- Customization: Whether you require threads, blind holes, through holes or flush bosses, we offer customization services to ensure that each machined boss is made to your exact specifications.
- Quality Assurance: Xavier’s stringent quality control measures ensure that each machined boss meets the highest standards. We inspect, measure and test to ensure dimensional accuracy and functionality.
- Efficiency and Reliability: We understand the importance of just-in-time production and component reliability. Our CNC machining services are designed to meet deadlines without compromising quality.
The importance of these real-world bosses across industries is self-evident. The average consumer may not notice their presence, but engineers and manufacturers understand the critical role they play in ensuring functionality, reliability, and safety across a wide range of products and systems.
boss machining is the unsung hero of precision engineering, providing stability, reliability, and functionality in countless applications.
Whether you work in the automotive, aerospace, manufacturing, robotics, or consumer products industries, a deep understanding of boss machining is key to engineering success. For businesses and professionals seeking high-quality boss machining, Xavier’s CNC machining services offer expertise and precision you can trust.