What is CNC Machine Metal Cutting? A Comprehensive Guide
In today’s fast-paced world, precision manufacturing plays a key role in creating complex metal parts with unparalleled accuracy and efficiency.
At the heart of this transformative process is CNC machine metal cutting. In this comprehensive guide, we’ll dive into the basics of CNC machine metal cutting, exploring its principles, techniques, and applications.
Whether you’re a seasoned professional in the manufacturing industry or a curious hobbyist looking to expand your knowledge, this guide will provide you with valuable insights and practical information to help you explore the world of CNC machine metal cutting.
1.What is CNC Machine Metal Cutting?
Computer Numerical Control (CNC): CNC technology is the foundation of CNC machine metal cutting. It involves the use of a computer system to control the movement and operation of the cutting tool. CNC machines interpret the instructions in a computer program and translate them into precise movements, ensuring accuracy and repeatability.

2.Advantages of CNC Metal Cutting
Compared to traditional manual cutting methods, CNC metal cutting has several advantages:
- Precision and accuracy: CNC machines can achieve high levels of precision and accuracy, ensuring consistent quality of finished parts.
- Efficiency and productivity: With the ability to automate operations and work continuously, CNC machines significantly improve productivity compared to manual cutting methods.
- Complex geometries: CNC machines excel at cutting complex shapes and precision geometries that are difficult or impossible to achieve manually.
- Repeatability and consistency: CNC machines can produce multiple parts with the same quality, reducing human errors and ensuring consistency.
- Versatility: CNC machines can perform a variety of cutting operations, including milling, drilling, tapping, engraving, etc., suitable for a variety of industries and applications.
3.Principles of CNC Metal Cutting
CNC metal cutting is based on several basic principles to accurately and efficiently remove material from metal workpieces. Here are the key principles:
- Not all metals can be cut: Some machines can cut tough metals such as steel, aluminum, and copper. However, not all CNCs can do this. The ability of a CNC machine to cut metal depends on various factors, including its rigidity, spindle power, the cutting tools used, and the machinability of the metal.
- CAD/CAM software: CAD (computer-aided design) and CAM (computer-aided manufacturing) software play a vital role in CNC machine metal cutting. CAD software is used to create a digital model or design of the desired part, while CAM software generates tool paths and cutting parameters based on the CAD model. These programs provide the CNC machine with the instructions it needs to accurately perform the cutting operation.
- CNC machine metal cutting tools: CNC machine metal cutting involves the use of a variety of cutting tools such as end mills, drills, taps, reamers, etc. These tools are mounted on a spindle, which rotates at high speeds to remove material from the workpiece. Choosing the right cutting tool depends on factors such as the material being cut, the cutting operation required, and the surface finish required.
- CNC Machine Metal Cutting Tool Paths: Tool paths define the trajectory and movement of the cutting tool during a cutting operation. These paths are programmed into the CNC machine using CAD/CAM software. The CNC machine precisely follows the tool paths to remove material from the workpiece to achieve the desired shape or design.
- CNC Machine Metal Cutting Cutting Parameters: Cutting parameters include variables such as cutting speed, feed rate, depth of cut, and tool engagement. These parameters are determined based on factors such as the material being cut, the type of cutting operation, and the desired results. Optimizing cutting parameters is critical to achieving efficient material removal and maintaining tool life.
- CNC Machine Metal Cutting Workholding: Workholding refers to the methods and devices used to securely hold the workpiece during the cutting process. Proper workholding is essential to ensure stability, accuracy, and safety. Common workholding methods include clamps, vises, fixtures, and chucks.
- Programming and Setup: CNC machine cutting requires programming the machine to perform specific operations. This programming is usually done using CAD/CAM software, where tool paths, cutting parameters, and dimensions are defined. Once the program is created, it is loaded into the CNC machine and the workpiece is clamped securely in place before the cutting operation begins.
There are many more principles that lead to an efficient CNC machine metal cutting process, these basic rules guide the process and form the basis for manufacturing precise, complex, and high-quality metal parts.
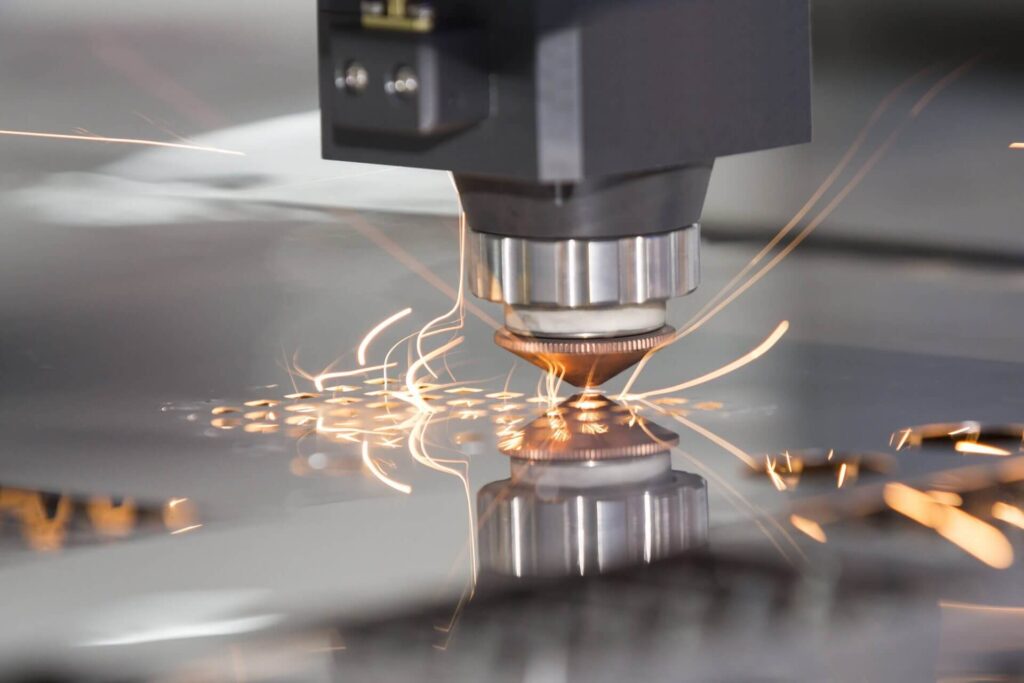
4.Types of CNC machine cutting operations
CNC machines are capable of performing a variety of cutting operations, including:
- Milling: In CNC machine milling, the cutting tool rotates while moving along multiple axes, removing material to create a flat or contoured surface.
- Drilling: CNC machines can accurately drill holes of varying sizes and depths in a workpiece.
- Turning: Turning operations involve rotating the workpiece while shaping it with a fixed cutting tool, and are typically used for cylindrical or tapered parts.
- Tapping: CNC machines can perform tapping operations to create internal threads on a workpiece.
- Boring: Boring operations can enlarge existing holes or create precise cylindrical holes with tight tolerances.
- Reaming: Reaming is used to achieve high precision and finish to existing holes, improving their surface finish and dimensional accuracy.
5.How to Make CNC Machine Metal Cutting Work Properly?
The process of cutting metal with a CNC machine is similar to other CNC metalworking operations. However, certain precautions must be taken to achieve clean cuts on metal workpieces.
1) Get a Rigid CNC Machine
If you want to cut metal on a CNC machine, the first step is to find a good machine that can do it. Entry-level CNC routers are better suited for softer materials, while CNC milling machines are ideal for cutting metal.
You can even make a DIY CNC machine yourself and use a powerful router that can handle softer metals, such as aluminum. But it is crucial to make sure that the CNC machine or DIY machine has a sturdy chassis to house all the components and provide powerful cutting capabilities without bending or buckling.
2) Securely clamp the workpiece: ensure stability
Before you start the cutting process on your CNC machine, it is important to ensure that the workpiece is securely clamped to prevent any movement caused by the cutting force. There are several clamping techniques available, including T-clamps, cam clamps, L-clamps, and double-sided tape. Double-sided tape is suitable for lightweight workpieces, while clamps are better suited for firmly holding metal workpieces.
In addition, vacuum beds can also be used for workpiece clamping. However, depending on the size and weight of the metal workpiece, a powerful vacuum pump is required. It is important to note that most CNC machine brands do not include a vacuum bed, so you may need to purchase one separately or create a DIY vacuum bed with your CNC machine.
3) Choose the right CNC machine metal tools
The tools used to cut metal during machining affect the surface finish and cutting speed of the cut. CNC machining involves various parameters that are directly or indirectly dependent on the choice of cutting tools, including speed, feed, depth of cut, and chip load. Therefore, durable cutting tools are required to provide strong cutting forces without breaking when machining metal.
For CNC metal machining, carbide end mills are often recommended because they are strong enough to provide strong cutting forces with minimal tool wear. The number of flutes on the end mill also affects the cutting process. Cutting tools with fewer flutes (such as 1 or 2 flutes) can easily clear chips, making them suitable for machining ductile metals such as aluminum and copper. On the other hand, cutting tools with more flutes can reduce chip clearance, resulting in smoother cutting.
4) Use adaptive cutting
When using CNC machining, the high-speed rotating tool comes into contact with the workpiece. This contact creates high impact loads that can damage the cutting tool or the workpiece. To avoid this, it is recommended to use adaptive tool paths or ramp tool paths.
These methods gradually increase the depth of cut, thereby reducing impact loads. By doing this, the life of the tool is extended while also producing smoother cuts and better surface finish.
5) Use cutting fluid
When machining metal workpieces, a lot of friction is generated, which generates excessive heat and damages the workpiece and cutting tool. It is important to use CNC cutting fluid to regulate the temperature of the cutting area and prevent overheating.
Cutting fluid also acts as a lubricant to reduce frictional heat and improve the cutting quality of metal workpieces. A typical coolant system consists of a reservoir, pump, and delivery hose to deliver the cutting fluid to the work area.
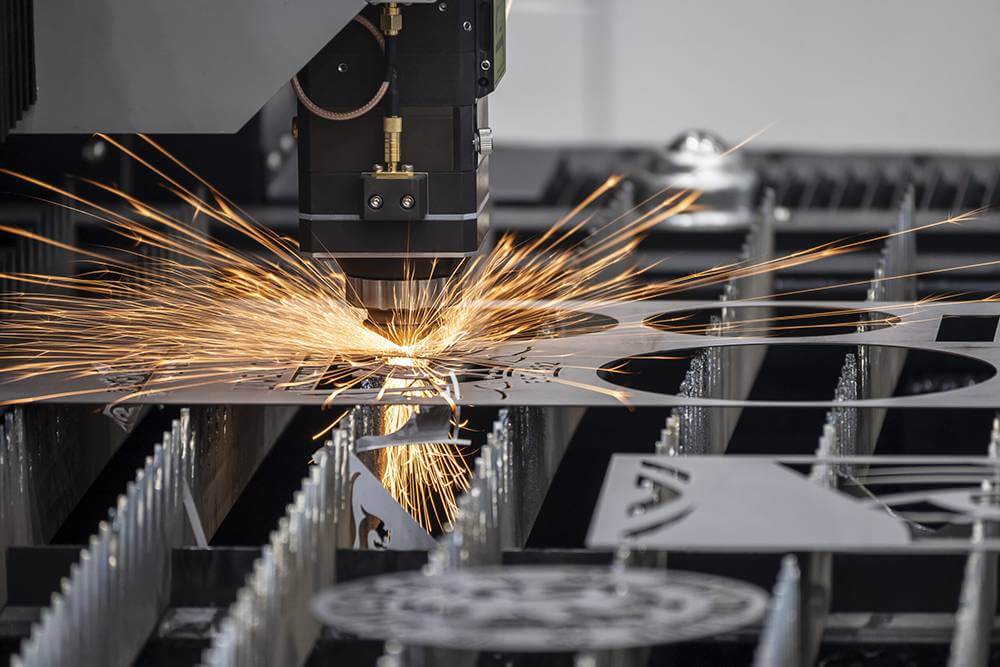
6.Final Words
CNC machine metal cutting has revolutionized the manufacturing industry by providing precise, efficient, and highly versatile cutting capabilities. Its ability to manufacture complex parts with superior precision has made CNC machine metal cutting an indispensable manufacturing method for various industries.
If you are looking for an experienced CNC machining manufacturer, Xavier is your ideal choice. The Xavier team is well-equipped to provide high-quality CNC machining solutions. If you need more information or to discuss your machining needs with us, please feel free to contact us.