Introduction to CNC milling
The first question that may come to your mind is what is CNC milling? It is one of the popular machining methods in modern manufacturing. Metal machining shops near me are almost all equipped with milling capabilities.
Like other standard CNC machining, milling refers to shaping compatible materials into the desired shape or geometry. However, the difference lies in the tools and capabilities.
Milling machines use a specialized tool called a milling machine with a rotating drill bit. The router moves over the workpiece following instructions (G-codes) and predetermined tool paths to form shapes to perform machining operations. Additionally, it involves a large CNC bed and low tool pressure. Therefore, routing operations are suitable for both thin and large sheets.
How does a CNC milling machine work?
The machine consists of a bed to hold the material and a spindle to hold the CNC milling cutter drill bit. First, the G-code is sent to the CNC controller and the drill bit is turned to the initial cutting position. At the same time, the operator sets machining parameters such as depth of cut, spindle speed, etc. Next, the spindle moves in multiple axes to remove material and create the desired shape, typically X horizontal, Y vertical, and Z height.
At this point, you may be wondering how a router controls the spindle. The spindle is connected with multiple motors and linear guides. Once the G-code is uploaded, the controller converts it into electrical signals that control these motors and rails. Here is the step-by-step process for CNC milling:
3D Modeling: This is the first step. The designer creates a detailed model that includes all specifications, features, and tolerances.
G-code: G-code is obtained by processing the 3D model into CAM software. It contains all processing information.
Machine Setup: In machine setup, a proper machine tool and CNC milling cutter are required to get the desired results. Likewise, secure the workpiece to the machine tool.
Zero positioning: The router bits are set at the starting position (0, 0, 0 reference).
Machining: The milling cutter rotates at high RPM and begins removing material along a predetermined path.
Monitoring: Processing continues to the final shape. Therefore, the process still needs to be observed for possible tool wear, accuracy deviations and other defects.
Surface Treatment: If the machined surface treatment is not sufficient for functionality or aesthetics, further surface treatment is performed, such as sandblasting, deburring, and brushing.
Quality Control: Final inspection and measurements ensure parts meet required specifications and standards.
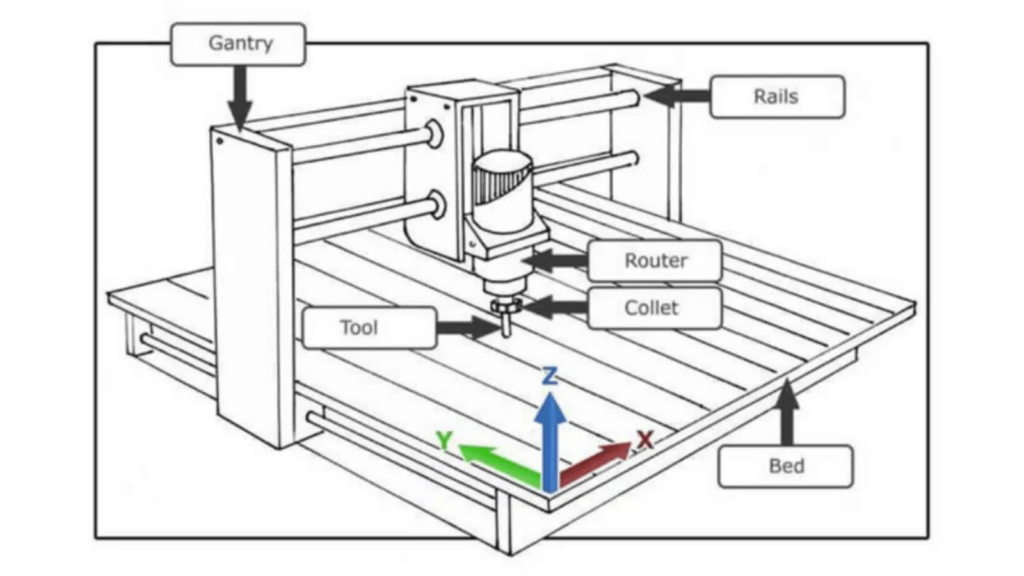
What are the main components of a CNC milling machine?
A CNC milling machine is a complex piece of machinery. It is composed of various components, each with a unique role and function. The cumulative effect of these components completes the CNC milling process. Here are the six main components:
- Frame and gantry
The frame is usually a stand with legs made of high-grade aluminum or steel. It resists cutting forces and damps vibrations, providing rigidity and stability to the machine. Likewise, the gantry structurally supports the movement of the spindle and cutting head.
2.Table or bed
They are flat surfaces with T-slots or vacuum fixing systems that allow the use of clamps and fixtures. Therefore, the workbench or lathe is responsible for safely placing and holding the workpiece for machining. Additionally, the bed contains tool path sensors or occasionally damaged MDF boards.
- Spindle
It is the component that provides the necessary cutting forces during CNC milling. Basically, a spindle is a rotating axis connected to multiple motors, bearings, and guidance systems for motion control. It also contains a collet or chuck that holds a cutting tool, such as a milling cutter, as it rotates and moves with the spindle. It can then spin at 10,000-20,000 rpm.
- Cutting tools
Routers allow the use of different cutting tools to achieve complex shapes and unique machining needs. Some milling kits include V-drills, ball end mills, drill bits, straight dressing bits, scrap board edgers, and more. Each of these tool varieties serves a different machining purpose. For example, straight drill bits are suitable for straight cuts and grooves, while V-shaped drill bits are suitable for engraving applications.
5.Shaft motor
As we all know, the spindle moves along multiple axes to perform milling operations. Therefore, axis motors achieve this through their precise coordinate and motion control. You can find two types of shaft drive motors: servo motors and stepper motors. The servo motor moves the gantry and spindle motor to the guide rail according to the G code instructions. They use feedback to continuously adjust speed and position. In contrast, steppers are simpler and move in discrete steps to control position and speed. Likewise, a rack and pinion system is connected along a longer axis, allowing the spindle or gantry to move along the X and Y axes.
- CNC controller
CNC controller is the electronic component of CNC milling machinery. It consists of a control processor (CPU), memory (RAM), input and output ports and drive circuits. The controller receives the G-code and executes it by sending electrical signals to the motor. Therefore, the motor (and eventually the spindle) moves according to the controller signal.
Common Types of CNC Milling Machines
There are many types of CNC milling machines based on size, functionality, and specific machining applications. Nonetheless, here we will discuss three main types: industrial routers, desktop routers, and multi-axis routers.
Industrial router
Industrial milling machines are suitable for heavy-duty manufacturing due to their high-power spindles. These are large and sturdy build machines that can handle intensive wiring projects. Additionally, they require more floor space than hobby or desktop routers. Additionally, industrial milling machines are essential in the woodworking, metal fabrication, aerospace, automotive, and marine sectors for processing a variety of parts quickly and accurately.
desktop router
Benchtop routers are efficient and powerful CNC machines that can move three or more axes. However, they are small and designed for space efficiency and ease of use. Due to capacity limitations, these routers cannot handle heavy industrial routing. However, benchtop CNC mills are perfect for small businesses, home workshops, and DIY milling enthusiasts.
Multi-axis CNC milling machine
For complex machining, there are routers with different axis capabilities. These machines have 3, 4 or 5 axis motion capabilities, and in some cases even more than 5 axes. As the number of axis movements increases, the machine can create more complex and precise parts. However, the choice depends on complexity, tolerances and workpiece material.