What is CNC milling: A complete explanation of the milling process
CNC milling is one of the most widely used CNC machining techniques. Milling is an ideal process for part manufacturing and surface finishing. It achieves high accuracy, repeatability, and output rate. Many industries use CNC milling, including the automotive, aerospace, robotics, and medical industries.
This article will introduce the CNC milling process and other milling basics such as definition, milling types, basic tools, and how to save costs through this process.
1.Definition of Milling
The term “milling” refers to any rotary tool-based machining operation used in the manufacturing process to remove material from a workpiece. Moreover, it is an adaptable method that can create a variety of forms and surface finishes in a variety of materials. It also involves the use of different types of machinery.
There are two types of milling operations: manual and automatic (CNC) milling. Manual milling refers to the traditional method of manually shaping and manufacturing items using hand tools and manually operated machinery. Getting the desired results depends mainly on the operator’s knowledge, proficiency, and experience. Here, we will discuss CNC milling in detail. Please continue reading.
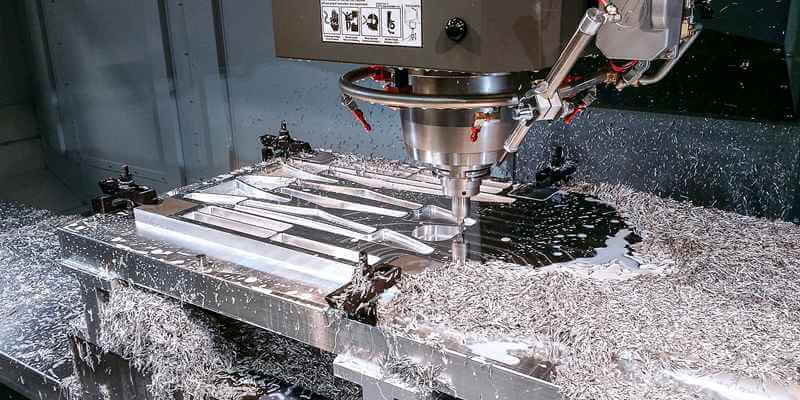
2.What is CNC milling?
So, what is CNC milling? CNC milling is a common machining technique where a computer-controlled device controls the operation. Milling uses rotating tools to cut materials such as plastic, metal, or wood. During CNC milling, the computer controls the spindle speed and feed rate, the order in which the tools are used, and the tool path of each tool.
The rotation of the cutting tool depends on the type of CNC milling machine and its complexity. Most CNC milled parts have a tolerance range of +/-0.001 inches to +/-0.005 inches. Some machines can even have a tolerance range of +/-0.0005 inches.
In addition, milling axis operations vary, ranging from 3, 4, 5-axis to multi-axis milling. 3-axis milling moves in the X, Y, and Z axes. In contrast, 5-axis milling machines move in the linear X, Y, and Z directions as well as the rotational A and B directions to produce more complex parts.
3.CNC Milling Axis Basics
CNC milling machines operate on two main axes: linear and rotary.
1) Linear Axes
CNC machines are based on the Cartesian coordinate system, which is widely used in mathematics and computer-aided design (CAD) software. The three linear axes in this system are perpendicular to each other and intersect at the origin.
These axes are the X, Y, and Z axes, which describe the orientation of the cutting tool. The X axis is the movement parallel to the cutting tool, moving from left to right. The Y axis is the movement perpendicular to the cutting tool, moving from front to back. The Z axis, on the other hand, is the movement from bottom to top.
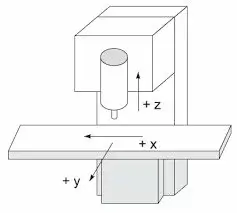
2) Rotational Axes
The name “rotational axes” comes from their connection to rotation. In addition, the relationship between rotational axes and linear axes is also obvious because these rotations always rotate around one of the three linear axes.
There are three rotational axes, and their relationship is usually shown below:
The tilt or rotation around the X axis is called the A axis, or tilt axis for short. The rotation around the Y axis is called the B axis, and the rotation around the Z axis is called the C axis.
4.How does CNC milling work?
It is essential to have a comprehensive overview of the milling process. This will help you fully understand how it works.
Typically, CNC milling operations are divided into three stages:
1) Design CAD Files
The first stage involves creating a virtual representation of the intended product using CAD software. You can use different CAD-CAM programs to develop the G-code required for machining. It is essential to convert the CAD design into the CNC programming language because this is what the machine can understand.
You can check and modify the code to meet the machine’s capabilities. The software also enables manufacturing engineers to simulate the entire milling process. Therefore, they can check for design errors and avoid creating complex models that are difficult to machine.
The operator also needs a technical engineering drawing that contains information such as:
- Dimensions and key features of the part
- Tolerances
- Construction lines
- Thread indications
- Finishing preferences
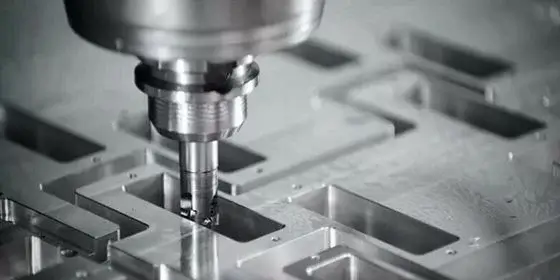
2) Setting up the milling machine
Although CNC milling machines can cut workpieces automatically, some aspects of the process still require a machine operator. For example, the operator must secure the workpiece to the table and attack the cutting tool of the spindle.
Modern milling machines have live tooling capabilities. Therefore, they are able to change tools during the milling process. This reduces the number of stoppages during operation. However, initial setup and program checks are still required before starting the process.
3) Production Components
As mentioned earlier, CNC milling uses a rotating tool that cuts off the chips when the tool contacts the workpiece. The continuous rotation of the tool achieves the desired shape. The process may contain different operations, depending on the type of raw material and the desired shape of the final product.
The first few processes use larger tools to carve the material and achieve an approximate shape. Then, changing the tool will help to create a more accurate machined part. Precision CNC milling is achieved in the final stages and involves unmatched surface finish and engineering tolerances.
5.Various CNC Milling Operations
CNC milling centers can produce a wide variety of complex features with high precision. These features include threads, chamfers, slots, etc.
However, creating these features requires various milling operations such as:
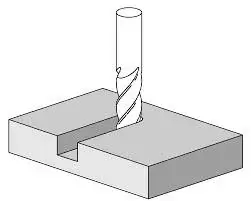
1) General Milling
Also known as surface milling, this operation uses a horizontal milling cutter. Therefore, the cutting tool has a rotation axis parallel to the table. Depending on the desired result, plane milling uses different cutters of different shapes and orientations.
A combination of wide cutters (faster feed rates) and finer cutting teeth (faster cutting speeds) is an excellent choice for cost-effectiveness. It also ensures better surface finish and a high-quality end product.
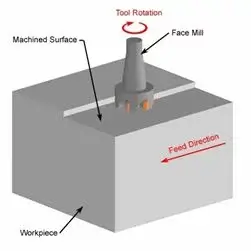
2) Face Milling
This type of milling uses a cutting tool that has teeth on both the side and the end. The teeth on the side are primarily responsible for the cutting work, while the other teeth at the tip are responsible for the surface finish. Face milling is usually performed after surface milling because it can create complex contours and leave a high-quality finish.
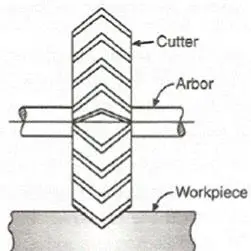
3) Angle Milling
This is one of the best milling operations for making grooves, chamfers, slots, and other complex features. Traditional 3-axis milling uses different cutters – a dovetail cutter for beveled slots or a tapered cutting head for making chamfers. The axis of the cutter is usually perpendicular or in line with the cutting surface.
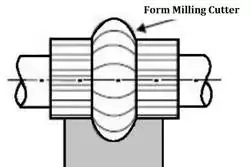
4) Profile milling
This milling operation uses special tools to create more complex contours. Concave and convex milling cutters are the most common here. They help create surface contours, round edges, and circular grooves in a single cut.
5) Other milling operations
In addition to the milling operations mentioned earlier, CNC milling machines can also complete other types of specialized milling operations such as:
- Profile milling: Here, the tool creates a cutting path along an inclined or vertical surface on the stock bar. This process uses a profile milling tool, which may be parallel or perpendicular to the workpiece surface.
- Combination milling: This is a subcategory of profile milling, using multiple cutters to create the pattern simultaneously. The cutters are usually of different shapes, sizes, or widths. They can perform similar or different operations to create more complex features or complex parts in less time.
- Cross-milling: This milling operation allows the machine to process two or more parallel workpieces with a single cut. Two tools are arranged on each side of the workpiece so that both sides can be milled on the same machine spindle.
6.CNC milling cutters that are essential in the process
While many CNC milling cutters are used, not all cutters are essential.
Here are some of the milling cutters that are essential to use.
1) Taps
A tap is used to carve threads in materials such as metal or plastic. They come in a variety of shapes and sizes, including manual and automatic taps. When attached to a milling machine, it can create threaded holes. In addition, this milling tap tool is ideal for use in softer materials such as plastic, brass, copper, and aluminum.
2) Drills
Drills mounted on a milling machine can be used to drill round holes in wood and metal. Drills come in a variety of shapes and sizes, including spade drills and twist drills.
In addition, drills are essential in CNC milling because they can accurately form a tapered hole before drilling, helping to prevent drilling the hole incorrectly.
3) End Mills
Cutting tools used for drilling and milling are called end mills. They are made of materials such as carbide or high-speed steel and come in a variety of sizes and shapes. Moreover, they can be used for a variety of cutting applications including side, face, bevel, plunge, and slot milling and are essential for shearing large amounts of material.
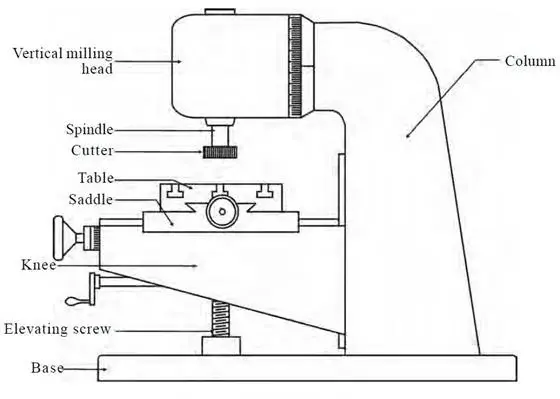
7.Components of CNC Milling Machines
Here, we will analyze the components that make up a CNC milling machine. Although new milling machines are a bit more complex, we will stick to traditional milling centers to provide a proper overview.
The basic components of a milling machine include:
1) Frame
This main structure supports the machine, giving it rigidity and stability. It has a base and removable columns. The machine headstock is an important part of the frame and is used to mount the spindle to prevent vibration or chatter during the operation of the machine. This prevents machining errors and prolongs the life of the cutting tools.
2) CNC Control Panel
You can call it the “nervous system” of the milling center. It consists of various electronic devices required to control different cutting actions using programming functions. The main components of the control panel are the CNC monitor and programming buttons. Most CNC milling machines come with an easily accessible control panel for easy machining.
3) Axe
CNC milling machines have X, Y, and Z axes. Depending on the configuration, they also come with additional rotary axes (A, B, and C). They are usually programmed using G-code in the CNC controller.
4) Column
This machine component provides structure and support to the other components of the milling machine. It comes with a fixed base and may include internal components that aid in the CNC milling operation. These internal components include coolant and oil tanks.
5) Table
This component is a solid base for holding the workpiece. In other words, it holds the stock bar, vise, or fixture in place. Depending on the milling machine used, this component can be adjusted vertically, horizontally, or bidirectionally. Most tables use T-slots to ensure easy clamping of the workpiece.
6) Spindle
The spindle consists of a tapered section that is used to position the tool holder. The spindle also has a rotating assembly and a shaft for holding the cutting tool. Depending on the type of milling machine, the spindle can be placed horizontally or vertically.
7) Arbor
This is the shaft assembly that is mounted on the spindle of a horizontal milling machine. They allow for multiple machine tools to be mounted. Arbors come in different lengths and diameters depending on the specifications required.
8) Ram
You will usually find this machine component in a vertical milling machine. It is usually mounted on a column that supports the spindle. The operator can adjust the ram to be in different positions during the milling process.
9) Machine Tool
This is the component that performs the material removal. There are several tools that can be used for milling, depending on the milling specifications. They vary according to arrangement, number, pitch, diameter, length, and geometry.
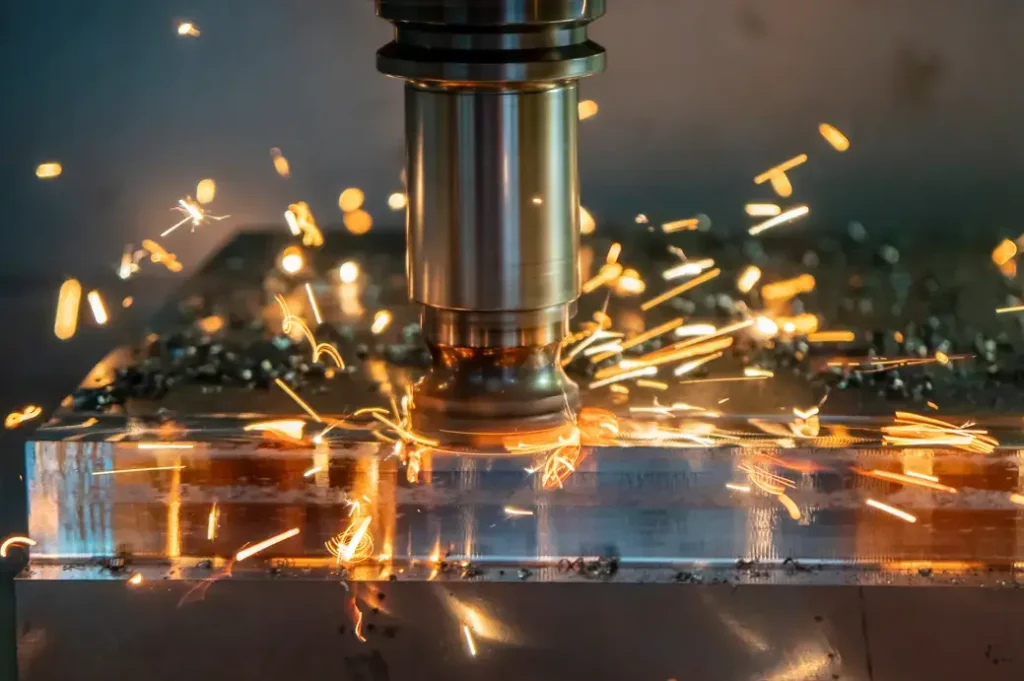
8.Types of CNC Milling Machines
Different types of CNC milling machines are suitable for different purposes. These machines include:
1) Vertical Milling Machine
This vertical milling machine has three axes of motion. It has a table that serves as a spindle and a table. As the name suggests, the spindle of a vertical milling machine is oriented vertically. Also, the spindle holds the axis of the tool as it rotates. There are two types of vertical CNC milling machines.
- Bed Milling Machines: Bed milling machines have a table that moves only perpendicular to the spindle axis. On the other hand, the spindle rotates in front of its axis.
- Turret Milling Machines: Turret milling machines have a fixed spindle and a table that can move parallel and perpendicular to the spindle axis. Some turret milling machines have a quill that can raise and lower the milling tool. Turret milling machines are more versatile.
2) Horizontal Milling Machines
The spindle axis orientation differentiates between vertical and horizontal milling machines. The spindle axis here is aligned horizontally.
Longer or heavier workpieces are best suited for horizontal milling machines. The rotating table on many horizontal milling machines enables the machine to grind at different angles.
3) Knee Type
The table on these machines can be adjusted vertically and is equipped with a fixed spindle. The knee supports the table while it rests on the saddle. The knee can be raised or lowered. Examples of knee-type milling machines include floor-standing, table-type, and regular horizontal milling machines.
4) Planer Type
They are similar to bed-type milling machines in some ways. Their table is set along the Z and Y axes. The spindle can move along the X, Y, and Z axes. Nevertheless, planer-type milling machines can support a wide variety of machine tools.
5) Bed Type
The table of a bed-type milling machine is fixed directly to the bed. The movement of the workpiece along the Y and Z axes is restricted.
In addition, bed-type milling machines can be divided into single-axis, dual-axis, and triple-axis. Dual-axis and triple-axis use two and three spindles, respectively, while single-axis, as the name suggests, has only one spindle that moves in the X or Y direction.
9.Different Multi-Axis Milling Machines
These machines can move along different axes and perform milling at different angles.
Common multi-axis milling machines can be:
1) 3-Axis Milling Machines
3-axis vertical milling machines allow the table to move along the X and Y directions. With these machines, the workpiece can be positioned relative to the cutting tool. The operator can then add the Z axis by lowering the cutting tool. CNC tools ensure that the three axes move simultaneously, providing the required flexibility for your needs.
2) 4-Axis Milling Machines
As mentioned above, these milling machines have all three axes. But there is another axis here – the A axis. The addition of another axis allows the table to rotate around the X axis. This provides room for face milling without repositioning the workpiece.
3) 5-Axis Milling Machines
All the advantages of the 4-axis milling machine apply here, but with the addition of the B axis. This addition helps the table rotate around the Y axis. 5-axis CNC milling machines are more expensive than the above options, but they allow complex parts to be produced in a single operation. They do not require additional setups and are compatible with dynamic tooling.
4) 6-Axis Milling Machines
Due to their high cost, 6-axis milling machines have not become standard. They have a fixed table with a cutting head that is completely free to move. That is, the cutting head can move along the X, Y, and Z axes.
10.Tips for Migrating Costs During CNC Milling
Here are some professional tips that can help reduce the cost and time of CNC milling projects.
1) Use Viable Materials
Machining time, the time it takes to produce a product, is as important to cost savings as material selection. Raw materials and part design are the main factors that determine machining time.
In addition, machining complex part designs with extremely precise dimensions is difficult and expensive. Choosing materials that are easy to machine whenever possible will help you address this issue. By choosing machinable materials such as brass, aluminum, and low-carbon alloys, you can also reduce the time required for machining. Hard metals such as steel are more difficult to machine and are prone to tool failure.
2) Use Tight Tolerances Only for Critical Features
For precision CNC machining, specifications are critical. However, finer tolerances in part design can significantly affect production costs.
For general features, it is recommended that you continue to allow standard tolerances. If necessary, you can define tolerances for some key features and functions. Likewise, keep milled hole sizes consistent. Deeper and smaller holes require more time to machine and can cause tool breakage, which leads to higher production costs.
3) Reduce Setup Time and Number of Setups
Each machined part goes through one or more operations. Each operation requires multiple preparations, including machine and material setup, part fixturing (if required), CAM programming (which varies depending on the cutting, milling, and drilling operations), and so on. Therefore, reducing the number of setups will help you avoid all the confusion and costs.
In addition, most parts can be completed in six setups or less. Whenever possible, reduce the number of required stages to one or two. The fewer the number of setups, the setup time will be reduced by half or more. In addition, this technique will enable you to machine CNC milled parts faster and more accurately.
4) Keep Internal Corners to Standard Radius
Internal corners also need to meet the requirements of standard specifications. Milling internal corners with small and precise radius is costly, time-consuming, and requires special equipment, especially when using very small tools. This is because workpieces are usually milled vertically by CNC machines.
For most machined parts, a suitable internal corner radius is 3 mm or ⅛ inch. Therefore, adhering to conventional radii can save setup costs and time for non-critical features.
11.Common Materials for CNC Milling Operations
CNC milling is suitable for a wide range of materials. The choice of material depends on the requirements and specifications of the application. The most common materials include:
1) Metal Materials for Milling
- Aluminum alloys
- Stainless steel
- Mild steel
- Tool steel
- Brass
- Copper alloys
- Titanium alloys
2) Plastic Milling Materials
- Polyoxymethylene
- ABS
- Nylon
- Polycarbonate
- Peep
- Polytetrafluoroethylene (Teflon)
- Polyethylene
- PMMA (Acrylic)
- High-density polyethylene
- PVC
- Polypropylene
12.Advantages and disadvantages of CNC milling in part manufacturing
The CNC milling process has become a necessity in various industrial processes due to its advantages. However, there are also some disadvantages. The following are some advantages and disadvantages of this manufacturing technology.
1) Advantages of CNC milling
① Accuracy and precision
The nature of the CNC milling operation minimizes the room for error, thereby ensuring higher accuracy and precision. The technology can produce parts that meet precise technical specifications and tolerance requirements.
Most CNC milled parts can have tolerances of +/- 0.001 inches to +/- 0.005 inches, while some parts can have tolerances of +/- 0.0005 inches. The automation of the process can also limit human error. Even if you need surface treatment, micro milling can remove some thickness to prevent affecting the size of the part.
② Efficiency and repeatability
CNC milling centers have high output due to the use of automation technology. Advanced milling machines can produce parts faster and with more consistent quality and finish.
③ Wide range of material compatibility
The process is suitable for a wide range of materials, including metals, plastics, glass and wood. This further increases its versatility, making it ideal for a variety of applications.
④ Reduced labor intensity
The automation and high output of CNC milling machines significantly reduce the labor required for the process. These machines also allow for real-time tool changes, ensuring that tools can be changed without stopping operations. The process requires minimal operators.
⑤ Cost-effective
CNC milling machines are able to produce complex products efficiently, quickly and accurately. This reduces the time spent in the production stage. In addition, less labor demand further reduces process costs.
2) Disadvantages of CNC milling
① High machine cost
The initial investment cost of CNC milling machines is higher than that of traditional manual equipment. This may drive up overall manufacturing costs.
② Intensive operator training is required
Not everyone can operate a CNC milling machine. From designers to programmers and machine operators, they all need to receive adequate training to fully utilize the process.
③ High level of maintenance
Milling machines must be constantly maintained to ensure their proper operation and extend tool life. This increases the downtime of the milling machine.
13.Which industries use CNC milling?
Many industries enjoy the benefits and multiple applications of CNC milling. Here are some of its industrial applications:
1) Aerospace Industry
The milling process is also suitable for manufacturing aerospace parts from materials such as aluminum and titanium. These materials are durable and lightweight, ensuring precise machining of the required parts.
2) Automotive Industry
The products produced in the automotive industry must be efficient and precise. Therefore, CNC milling is suitable for producing interior panels, drive axles, cylinder heads, gearboxes, exhaust components, suspension components, etc.
3) Medical Industry
Medical and surgical tools often have unique designs that require optimal precision. This makes CNC milling one of the best ways to manufacture such parts. This way, the design is preserved and efficiency and productivity are also improved.
4) Consumer Products
CNC milling operations also help in the production of common parts. These parts include nuts and bolts, gears and shafts, flanges, etc. The process is suitable for both small and large-scale production.

14.Alternatives to Milling
1) Grinding
Grinding can remove harder materials and produce products with finer surfaces and tighter tolerances than milling. Many products are CNC milled before grinding, but some are ground entirely from stock using a technique called abrasive machining.
Grinding is often chosen over milling when little metal needs to be removed and surface smoothness and dimensional accuracy are critical.
2) Planning or Shaping
The starting cost of a milling machine is significantly higher than a planer or router that can also machine the same size workpiece. In addition, setup times are generally longer and milling cutters can cost up to 50 times more than other types of equipment.
Planing uses a single-point cutting tool to remove material from a workpiece. It can also effectively remove large amounts of material in a linear motion. However, this process is difficult to machine precision parts.
3) Broaching
This machining technique uses a sharp, hardened, toothed tool to continuously and accurately remove material from a workpiece. In broaching, a tool with different sized raised teeth is used to remove an accurate amount of material with each pass.
Broaching is sometimes more cost-effective than milling when machining large quantities, but it also has disadvantages. Some of the disadvantages are that it is a slower process and a bit difficult when machining harder or stiffer materials. Also, setting up the machine can be time-consuming compared to milling.
15.Future Trends in CNC Milling
Today, modern production relies heavily on CNC milling, and as technology advances, more trends and developments will emerge in this field. One recent advancement is the increased versatility of CNC milling machines, which makes them ideal for processing a wider range of materials.
In addition, CNC milling machines and software are also becoming easier to use. This is due to the increased computing power of CNC machines, which reduces human involvement.
At the same time, workstations with more powerful processors can help speed up the modeling and design work required to create the templates that CNC milling machines use as the basis for their operations. Therefore, every link in the chain benefits from technological developments and time savings.
16.Conclusion
CNC milling is suitable for a wide range of high-quality applications, regardless of their complexity. This cost-effective manufacturing process also saves a lot of time, ensures operational efficiency, and speeds up product launch.
If you are looking for an experienced CNC machining manufacturer, Xavier is your ideal choice. The Xavier team is well-equipped to provide high-quality CNC machining solutions. If you need more information or to discuss your machining needs with us, please feel free to contact us.