What is CNC Turning? Process, Benefits and Applications
CNC turning has made it easier to machine parts that were difficult decades ago. The technology is precise and ensures consistency in producing high-quality parts. It uses a fixed cutting tool to remove material from a rotating workpiece. As a result, it can produce components of different shapes and sizes that meet tight specifications and tolerances.
Understanding the basics of precision CNC turning is essential to maximize its benefits and increase productivity. This article provides answers to all your questions about CNC turning. It will explain in depth the turning manufacturing process, the types of operations that can be used, and the applications of CNC turned parts in the manufacturing industry.
1.What is CNC turning?
CNC turning is a subtractive machining process that removes material from a workpiece that is rotating at high speeds. The workpiece is fixed to a chuck that rotates at varying numbers of revolutions per minute. When the cutting tool comes into contact with the rotating workpiece, it removes material and carves out the desired shape.
CNC lathes primarily process cylindrical or rectangular parts. It can also be used to make other shapes such as discs, cones, hexagons, or mixed shapes.
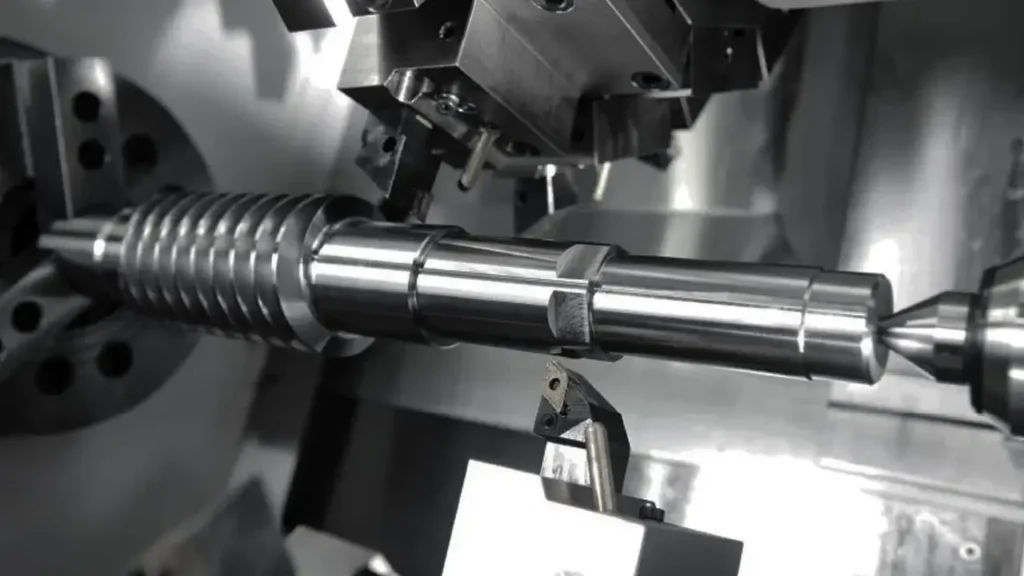
2.How to Operate a CNC Lathe
The turning manufacturing process is simple. It is divided into the following 4 stages:
1) Create a CAD Model
The first step in CNC turning is to prepare a 2D or 3D model of the final design using CAD software. There are many types of software that can be used. SOLIDWORKS, Fusion 360, and AutoCAD are the most common. It is easy to prepare a CAD model for a simple design. However, more complex designs will require the services of an expert.
2) Convert to CNC Compatible Format
The next stage is to convert the electronic design into a language that the machine can understand. You can do this using CAM software such as Mastercam, solidCAM, or CAMWorks. CAM software checks the model for any errors, provides directions for the turning tool, and sets the necessary machine parameters.
3) Prepare the CNC Lathe
Before you can perform a turning operation, you must set up and configure the machine. Despite automation, the operator still plays a vital role in preparing the CNC lathe. To do this,
- Turn off the machine and load the workpiece onto the chuck.
- Then, select the tool and fix it on the turret.
- Perform calibration by setting up the tool and workpiece correctly.
- Check and optimize the necessary parameters.
- Upload the CNC code and prepare for turning operations.
Note: For rough shapes, lower turning speeds and higher feed rates are better. For smoother surfaces and parts with precise tolerance requirements, higher turning speeds and lower feed rates should be selected.
4) Producing CNC turned parts
Now, it is time to bring your idea to life. There are many turning operations that can be used. Once a program is executed, the machine runs continuously until the program ends or it is turned off. Loading, cutting, and idle time determine the turning cycle time. You may need to run the machine multiple times. This depends on the complexity of the part.
3.Types of CNC turning operations
CNC lathe machining operations can be either internal or external machining. External work is used for the outer diameter of the workpiece, while internal work is used for the inner diameter. However, internal machining is more difficult. It causes more chip accumulation and requires longer tools.
Let’s look at these two categories of CNC operations in detail:
1) External Turning Operations (Specific)
① Turning
During turning, the tool gradually removes material along the side of the workpiece to reduce the outer diameter. This operation can be either roughing or finishing. In rough turning, the final part is precise and has a rough surface. However, the surface of the final part in finishing turning is fine and shiny.
In addition, the surface of the turned part can have a variety of features. It can be steps and tapers, or chamfers and contours.
② Hard Turning
Hard turning is similar to normal CNC turning operations. However, experts reserve it for hardened steels with hardness values between 58 Rc and 68 Rc. Single-point inserts produce precision parts that meet the industry’s tight tolerances. Hard turning is an alternative to CNC grinding. Compared to grinding, hard turning is efficient, fast, and affordable.
③Facing
Many times, workpieces are often longer than they should be. Face turning is designed to reduce the length of a part. In face turning, the end of the workpiece is perpendicular to the axis of rotation and moves along the tool. This process smooths the part while producing the desired length.
④Grooving
Grooving operations involve making narrow cuts in the workpiece. The size of the cut is related to the width of the cutting tool. The wider the tool, the larger the groove that can be produced. Very large grooves require multiple passes and longer times. Note that the grooves can be on the outside or surface of the workpiece.
⑤Parting
During the parting process, the cutting tool moves radially to the side of the workpiece. When the tool reaches the inner diameter or core, it cuts off or removes a portion of the raw material. This operation is suitable for parts that have been machined to the desired shape and size.
2) Internal turning operations (non-specific)
①Boring
Drilling involves rotating the pre-drilled workpiece on the blade. As the part rotates, the blade cuts into the edge of the hole to form various features. Drilling operations help enlarge smaller holes, straighten holes, and cover up die casting defects.
② Drilling
Drilling uses a drill to bore a hole in a workpiece by slowly removing excess material. The size of the drilling tool will determine the diameter of the hole. It is important to properly calibrate the CNC lathe to ensure accuracy.
③ Threading
This operation uses a specialized threading tool with an indexable insert that moves axially along the side of the workpiece. This tool has a 60-degree tip angle that cuts threads on the outer surface. Thread lengths vary, and some may require multiple machining.
④ Knurling
The knurling operation on a CNC lathe creates patterned ridges on a metal workpiece. These serrated patterns are practical because they enhance grip. It also serves an aesthetic purpose, improving the appearance of the part.
⑤ Reaming
Reaming uses specialized tools to enlarge a pre-drilled hole and improve its surface finish. It is similar to boring and drilling. However, it removes less material and is primarily used as a post-processing technique.
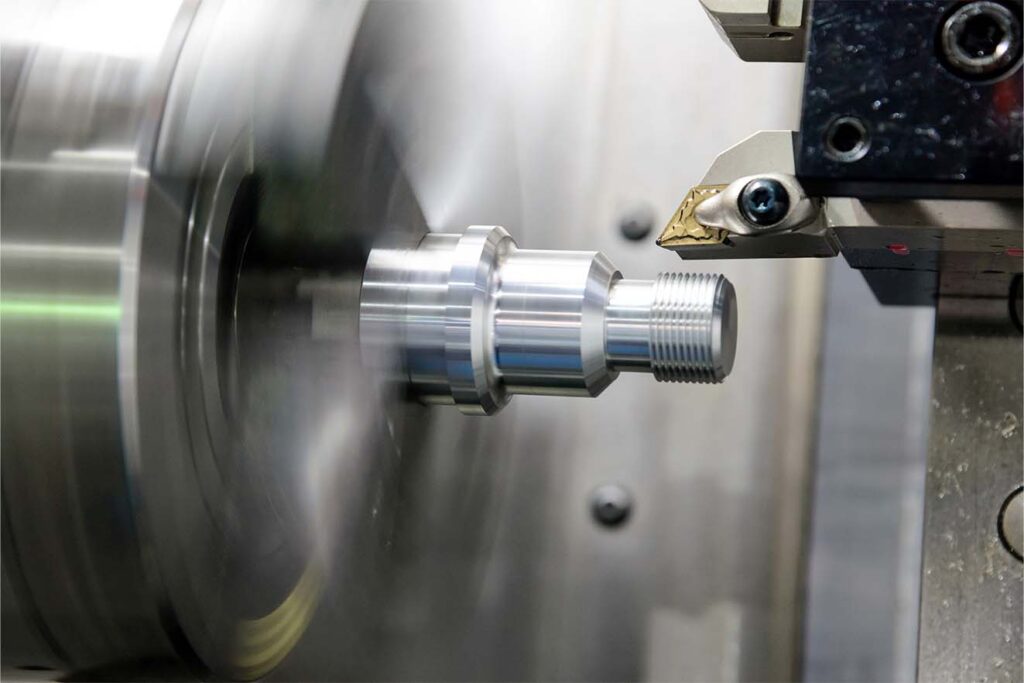
4.Types of CNC Lathes
There are four main types of CNC lathes you can use for your project. They include:
1) Horizontal Turning Center
It is an enclosed machine that uses a horizontal spindle. As the workpiece rotates, the cutting tool shapes it. It is more suitable for long and cylindrical parts. This type of CNC turning center is not affected by gravity. Therefore, chips accumulate around the cutting tool and may be difficult to remove. This machine type can be used to make precision tools and custom automotive parts.
2) Vertical Turning Center
Here, the workpiece rests on a vertical spindle. The cutting tool also works vertically to machine the part in an upward or downward direction. This type is suitable for complex parts as it contains additional milling and drilling features. It has extensive use in structural applications and creating prototypes for experimental purposes. The vertical orientation of this machine type helps in easy chip removal and faster tool changes.
3) Horizontal Lathe
Here, the workpiece rests parallel to the ground as the spindle is in a horizontal position. This machine has a small load capacity and limited rigidity and is suitable for machining small and medium-sized components. It can achieve tight tolerances when producing electrical accessories and medical devices.
4) Vertical Lathe
Compared to horizontal lathes, here the spindle is in a vertical position. This is a perfect choice for workshops with limited space. The machine has excellent load-bearing capacity and is suitable for machining heavy parts such as ship and wind turbine components. The vertical setup adds flexibility to machining practices to accommodate different space and weight requirements.
5.CNC Lathe Components
It is important to understand how each component of a CNC lathe works to achieve the best results. Here is how a CNC lathe works:
1) Headstock
The headstock is the power source of a CNC lathe. The headstock houses the spindle that rotates the workpiece. The headstock moves along the X-axis and is located on the left side of the machine. The headstock determines the maximum workpiece diameter that can be machined.
2) Tailstock
The tailstock is located at the other end of the headstock and moves along the same axis. Its main function is to support longer workpieces and prevent them from deflecting.
3) Spindle
Experts call the spindle the backbone of a CNC lathe. It holds and rotates the workpiece. Most machines have only one spindle. However, some machines have more than one spindle to complete machining operations.
4) Chuck
The chuck is an important part of the machine tool as it holds the workpiece while it is being machined. The chuck is mounted on the headstock and is rotated by the spindle. As it rotates, the workpiece moves in the same direction.
5) Lathe Bed
This is the base of the machine where the workpiece is mounted. It serves as a foundation to support and attach other components. Usually, it has holes that the machinist can use to attach workholding fixtures. This ensures that the workpiece stays in place and avoids errors.
6) Carriage
The tool holder mounts and controls the movement of the turning tool. It supports the turret and guides it onto the workpiece. The main parts of the tool holder are the turret, cross slide, and saddle. The tool holder moves along the bed relative to the workpiece.
7) Turret
The turret is the tool holder. They can hold multiple tools at the same time in the correct sequence. This allows for quick changes of cutting tools and reduces the number of steps required to machine a part.
8) Control Panel
This is the brains behind all CNC turning operations. The control panel interprets the G-code and converts it into instructions. It determines the position of the tool and enables the operator to adjust the program before starting the machining process.
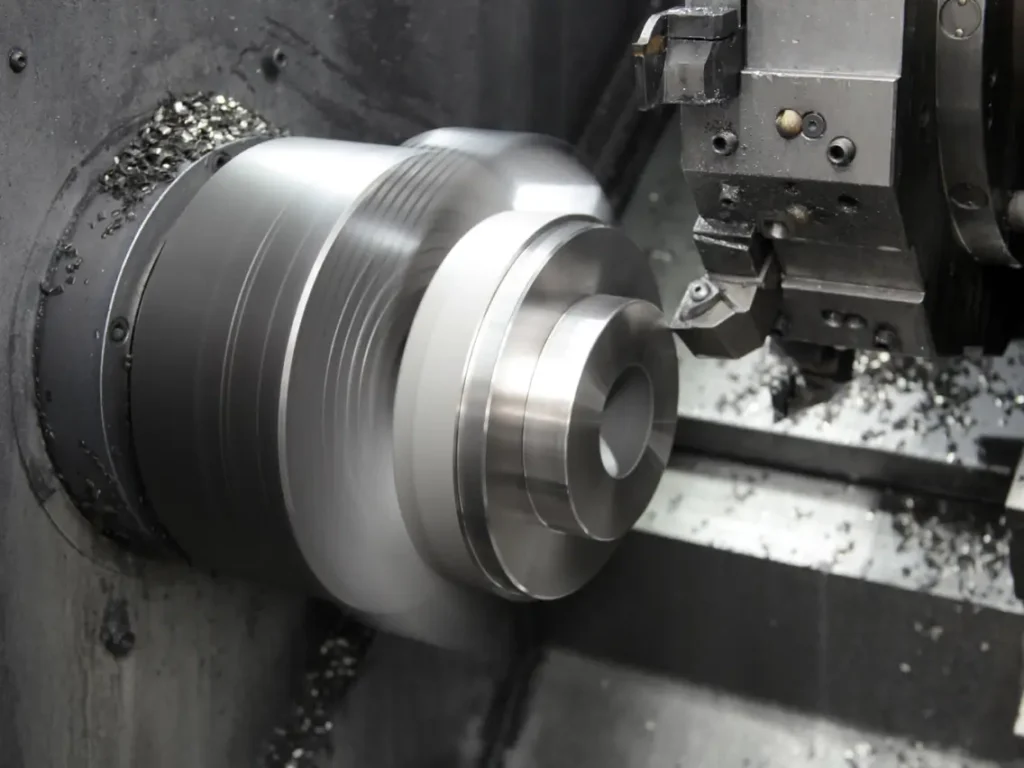
6.Advantages of CNC Turning
There are many advantages to the CNC turning process, which include:
- CNC turning eliminates human error through the use of CAD and CAD software, so it can produce precise parts.
- Turning centers are compatible with a wide range of materials and parts of different sizes, which provides flexibility in manufacturing.
- CNC lathes are efficient and fast, allowing parts to be marketed on time without compromising quality.
- In addition, CNC turning is a precise method because it ensures consistency in production batches.
- Turning is a safe process because it is completely enclosed, which prevents material from flying around.
7.Disadvantages of CNC Turning
Despite the numerous advantages of CNC turning, there are also some disadvantages. Here are some disadvantages of the turned part manufacturing process:
- It is costly to set up and maintain a CNC lathe.
- CNC lathe processing has size limitations and may not accommodate very large workpieces.
- Since turning is a subtractive processing method, it produces a lot of scrap.
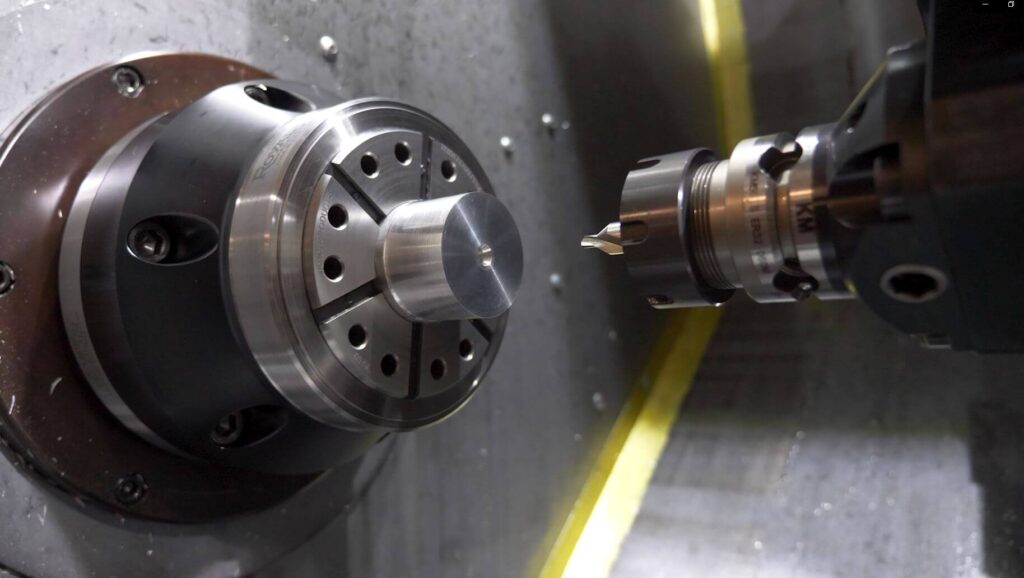
8.What are the best materials for CNC turning?
CNC turning can process a wide range of materials to provide a high-quality final part. Different materials require specific considerations in terms of turning speeds, feed rates, and tooling. Here is a breakdown of some common precision CNC turning materials:
1) Metals
Most CNC turned parts are made of metal because metal is strong and can withstand rigorous operations. Machinists often use brass, aluminum, titanium, and steel.
2) Plastics
Plastics such as nylon, ABS, PTFE, and acrylic can be used for CNC turning. They are lightweight, strong, and easy to machine.
3) Wood
Precision CNC turning can also process woods such as walnut, oak, and maple. The process can produce fine artistic wood products with a flawless finish.
4) Glass
While glass may not be as common as other materials, it is viable in some CNC turning applications. Using the right parameters, different types and thicknesses of glass can be processed.
5) Wax
Wax can be used for prototyping using the CNC turning process. It is low-cost, easy to cut, and can quickly produce detailed prototypes.
9.Applications of CNC Turning
CNC turning is an important process in the manufacturing industry. Almost all cylindrical and conical parts are the result of this process. This section will briefly discuss some industries that rely heavily on CNC turning.
1) Aerospace Components
CNC turning has revolutionized the aerospace industry. It is a very valuable method because it can produce lightweight aerospace parts with zero tolerance. Manufacturers use turning when producing threads, screws, shafts, connector pins, and nuts.
2) Automotive Components
CNC turning plays a vital role in the automotive industry. It is repeatable, speeds up production, and promotes sales. CNC lathes are very useful in manufacturing automotive parts such as cylinder blocks and dashboard components.
3) Electronics Industry
Since no special tools are required, CNC turning helps produce parts for the electronics industry in a short time. It is compatible with metals and plastics and can be used to manufacture research electronic components.
4) Oil and Gas Industry
Precision CNC turning helps in manufacturing, repairing and maintaining parts for heavy machinery in the oil and gas industry. It is the most reliable and accurate method for manufacturing parts such as pins, pistons, rods and cylinders.
10.Conclusion
CNC turning is essential in the manufacturing industry and provides precision and versatility for a wide range of components. This article describes the different types of turning machines available, CNC turning operations, and their advantages and disadvantages.