Surface treatment:A Comprehensive Guide for Manufacturers
In the manufacturing process of metal parts, surface treatment is undoubtedly a crucial link. Not only can it significantly improve the performance of metal parts, it also has high aesthetic value. This article will give you a detailed and in-depth introduction to the importance of surface treatment, common processes and outstanding advantages.
1. What is surface treatment?
Surface treatment refers to the process of modifying the metal surface to improve specific properties. Its main purpose is to enhance the metal’s corrosion resistance, durability, adhesion, or significantly improve its appearance.
2. why is surface treatment important?
1.Protective effect
Surface treatment can protect metal parts from rust, heat, weathering and pressure, extend the life of parts and reduce maintenance and upkeep costs.
2.Functional improvement
Improve the functionality of metals, such as thermal protection or conductivity for specific areas, and give metal parts more application value.
3.Aesthetics
The parts can be treated according to their desired appearance, making the product more beautiful and attractive, and improving the market competitiveness of the product.
3. Commonly used surface treatment processes
Ⅰ、Electroplating
Immerse the metal parts in an electrolyte solution containing a metal coating, and pass an electric current to make the metal parts obtain nickel plating, zinc plating, chrome plating and other coatings.
Advantages:
1.Improve corrosion resistance, such as nickel plating and chrome plating can enhance corrosion resistance.
2.Improve hardness to prevent automotive parts from losing their luster.
3.Metallize plastic parts, conduct electricity, improve appearance, and improve durability.
4.Enhance performance to meet the thermal protection or conductivity requirements of specific areas.
5.Improve aesthetic effects and make products more beautiful.
6.Extend the life of metals and plastics and reduce raw material consumption.
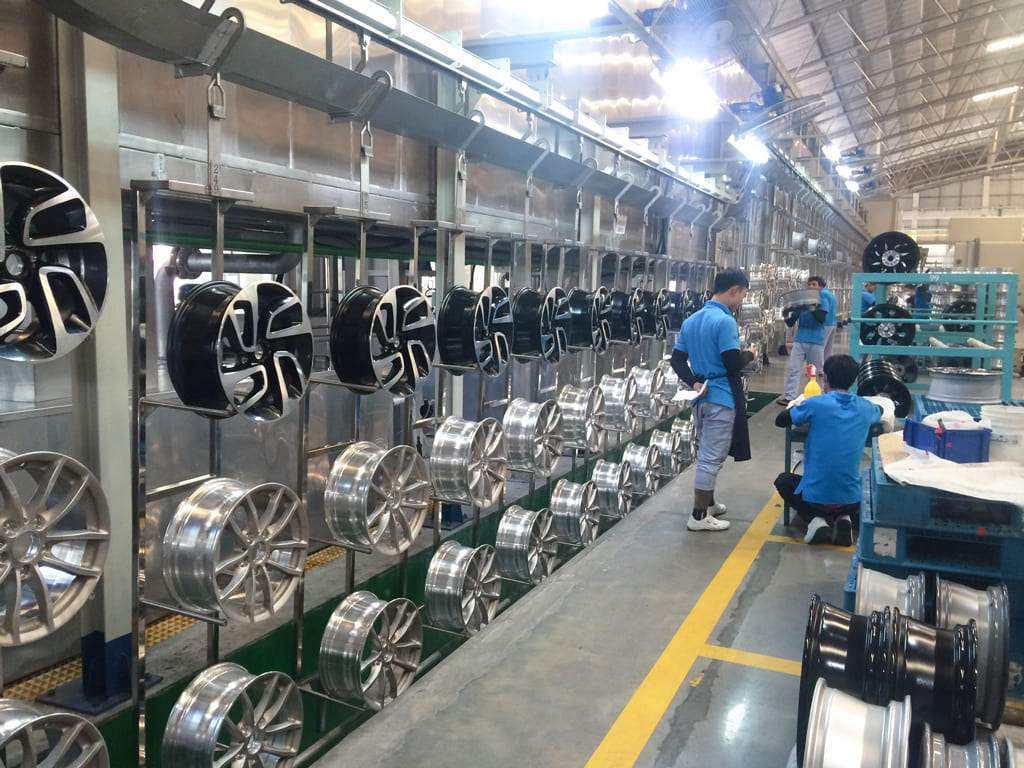
Ⅱ、Anodizing
An electrochemical process in which a metal part (usually aluminum) is immersed in a bath filled with an acidic electrolyte, creating a natural oxide layer on its surface that acts as a protective coating.
advantage:
1.Strong durability, strong combination with aluminum, and unparalleled adhesion.
2.Stable color, long service life and significant economic advantages.
3.Easy to maintain, simple to clean dirt.
4.Beautiful, providing a large number of gloss and color options, maintaining a metallic appearance.
5.Low cost, low initial cost and maintenance cost.
6.Healthy and environmentally friendly, harmless to the human body, and stable in surface chemical properties.
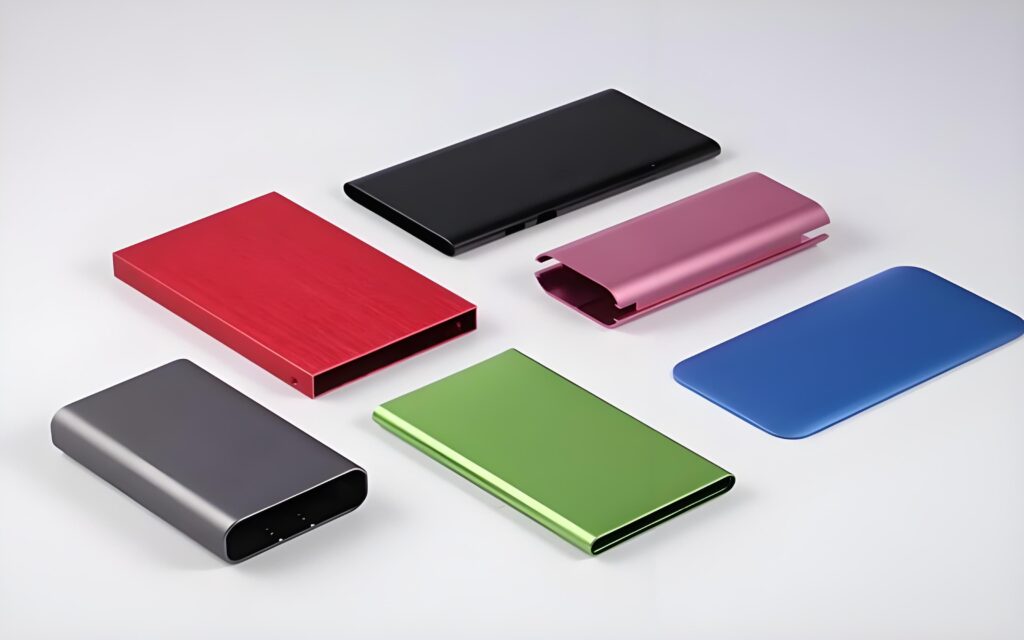
Ⅲ、Powder Coating
The workpiece is charged with an electrode, and the oppositely charged powder is sprayed onto the workpiece, and then placed in an oven to melt the dry powder and bond with the surface.
Advantages:
1.A variety of plastic resins can be used to utilize different materials.
2.Strong durability, one of the hardest surface treatments, with a service life of 20 years or more.
3.Add multiple advantages such as wear resistance, chemical resistance, electrical resistance, etc.
4.The coating thickness and quality are good, smoother, thicker and uniform in thickness.
5.Environmentally friendly, avoid the use of toxic solvents, produce less waste and can be reused.
6.Rich colors, special effects can be achieved, and any color can be matched.
7.Short curing time and high production efficiency.
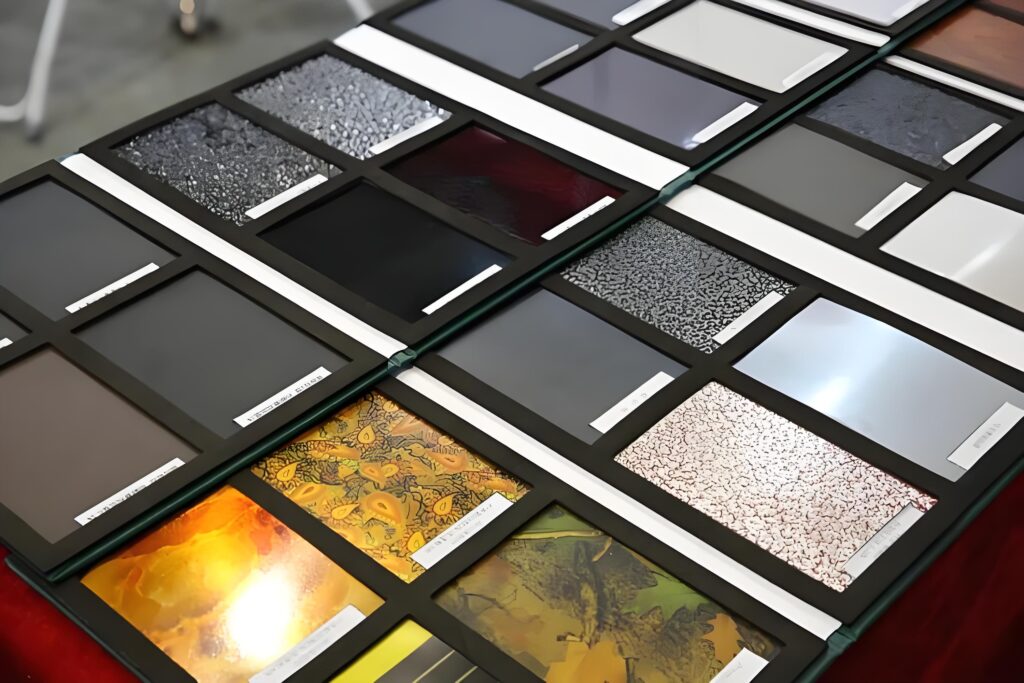
Ⅳ、Thermal spray coating
Use a torch and raw materials (wire or powder) for spraying. After melting the raw materials, spray them onto the surface at high speed to form a coating.
Advantages:
1.Reduce costs. Repairing objects is cheaper than replacing them, and it is efficient and less wasteful.
2.The coating materials are wide-ranging, including metals, alloys, ceramics, plastics, etc., which can be specially selected according to the substrate.
3.Applicable materials are diverse. Almost all materials that can withstand heat can be sprayed.
4.Extend the life of the material and provide an effective barrier to prevent surface damage.
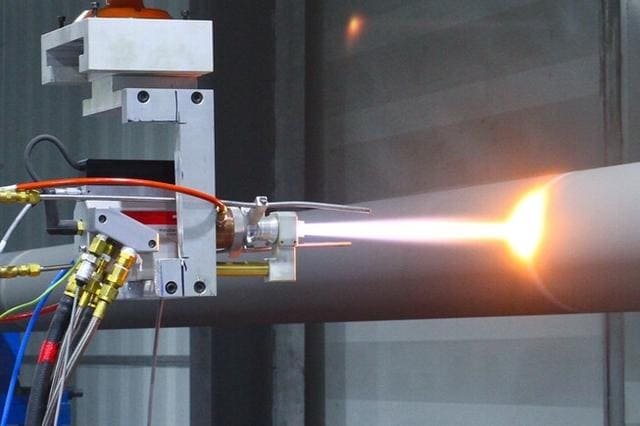
Ⅴ、Sandblasting
Abrasives are projected onto the surface at high speed to make the surface clean, smooth or rough.
Advantages:
1.Removes scale, oil and rust from the surface of steel parts.
2.Abrasives can be reused to reduce costs.
3.Removes a variety of harmful surface contaminants.
4.Speeds up the cleaning process and reduces manpower requirements.
5.Effectively removes old paint and prepares for new paint.
6.A variety of abrasives are available and can be selected according to needs.
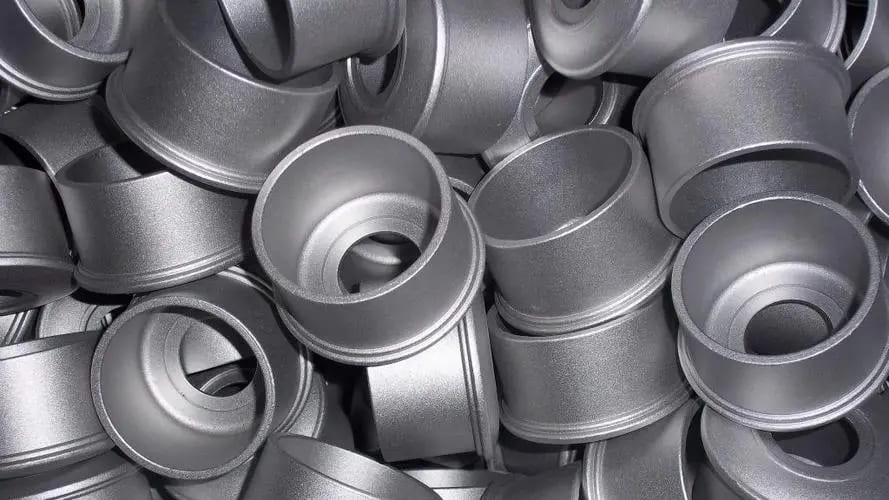
4. Summary
In the field of metal parts manufacturing, surface treatment plays a crucial role, which can significantly improve the performance and aesthetics of metal parts. This article provides an in-depth look at commonly used surface treatment processes. Each of these processes has unique advantages and plays a key role in the manufacturing of metal parts. Processors can make reasonable choices based on their own needs.
If you are looking for an experienced surface treatment processor, Xavier is undoubtedly your best choice. The Xavier team is well-equipped and specializes in various surface treatment solutions, which can fully meet your personalized processing needs. For more information or to discuss your processing needs with us, please feel free to contact us.