What is Swiss Machining Services: How it works and its benefits
Swiss machining is a part manufacturing process that is often used to make tiny parts such as watch components. It originated in the Swiss watchmaking industry but is now used in several industries around the world.
This article will extensively discuss the process, its mechanism, characteristics, comparison with other manufacturing processes, and overall use in part manufacturing.
1.What is Swiss machining services?
Swiss machining is a set of manufacturing techniques, such as Swiss turning and milling, that use specialized tool cutting machines to process metal raw materials into the desired parts. It uses Swiss machines to make extremely small parts with very tight tolerances.
The first Swiss machines were traditional, i.e. they did not have a computer control center. However, there are now Swiss designed CNC machines. Therefore, some people use the term “Swiss CNC machining” to describe its use in the CNC industry.
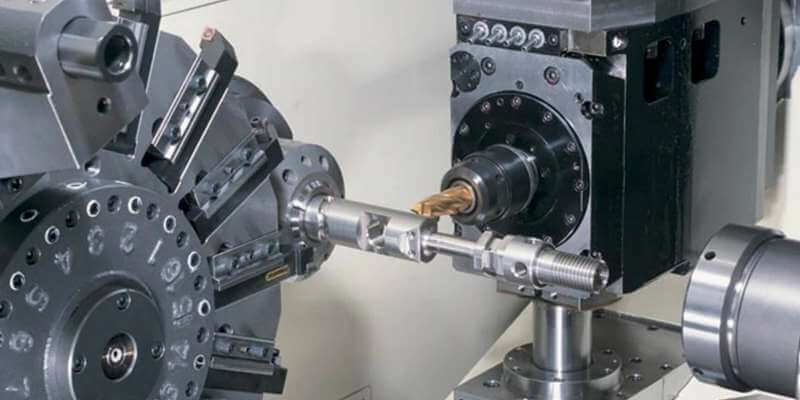
2.How does a Swiss machine work?
Swiss machines have many names, such as Swiss screw machines and Swiss lathes. Their unique design makes them highly precise and accurate.
The machine has multiple axes and, unlike traditional CNC machining, is able to rotate and move back and forth along the Z axis. The operator feeds the bar stock into a guide bushing (which has a cutting tool installed).
Due to this arrangement, the guide bushing provides strong support regardless of the length of the workpiece. The force is located exactly where the material emerges from the guide bushing, which minimizes the action of the tool on the part and improves accuracy. In addition, it allows you to perform multiple operations at once.
3.Advantages of Swiss Precision Machining
Swiss precision machining has some advantages that make it more suitable for certain applications than other part manufacturing technologies. Most of the time, the industry prefers to use this process because of its high accuracy, technical level, and standard features.
If you choose this process, you will get some of the following benefits:
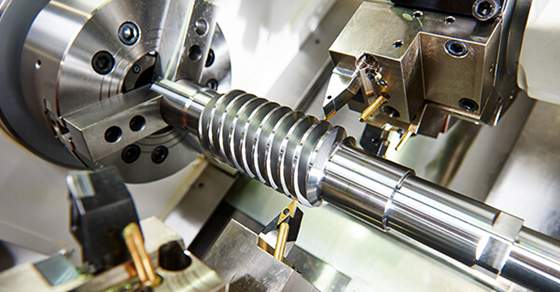
1) Efficiency
Swiss machines have multiple axes that allow you to perform multiple operations at the same time. Therefore, they are efficient compared to other lathes without considering the complexity of the part design.
2) High Precision
High accuracy makes it suitable for manufacturing parts with complex shapes and tight tolerances. In addition, its action mechanism ensures that the tool force does not affect the workpiece, thereby improving accuracy.
3) Suitable for Small Parts
The machining process was originally used to process small parts such as electronic parts and watches. Although this has improved due to technological advances, technological advances have expanded its applicability to small parts. In addition, the high level of automation reduces human intervention or control.
4.Comparison between Swiss machining and conventional machining
The main difference between Swiss machining and conventional machining is that conventionally machined parts are generally not as precise as Swiss machined parts.
Swiss machines have high precision, while conventional machining relies more on the steady hands and mind of the operator. Therefore, accuracy and repeatability are lower.
Another difference between the two machining methods is that conventional machining is better suited for machining regular parts, while Swiss machining is effective for handling complex designs.
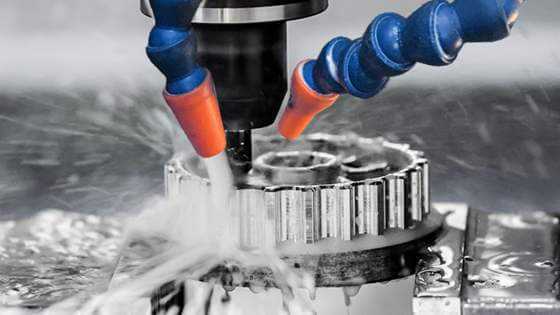
5.Comparison between Swiss machining and CNC machining
Swiss machining and CNC machining are similar in many ways. However, Swiss machining has its own advantages compared to CNC machining (DFM process).
Although we can also say that they both use programming languages such as g-code and m-code. Now the question is, what is the difference in the CNC machining process? Here are four differences between Swiss machining and CNC machining. Let’s explore them:
1) Shorter production cycle for highly complex parts
Modern Swiss lathes have about 7 to 13 axes. Therefore, it can perform multiple operations on a part faster in one machining cycle. These operations include drilling, face grooving, Swiss milling, thread cutting, cut-off, and more.
However, conventional lathes such as CNC lathes have only 3 to 5 axes and may not be able to complete the machining of parts in one cycle, so the cycle time of CNC lathes is shortened and productivity is limited.
2) Coolant Type
Swiss-type lathes usually achieve better tolerances due to their coolant properties. In most cases, Swiss machines require oil to operate better. Unlike water, oil has a lower heat capacity.
Therefore, Swiss machining can transfer heat away from the cutting edge of the tool and cool it easily compared to CNC.
3) Segmented Machining
Unlike CNC machining, Swiss machines such as Swiss lathes produce parts in segments. This is very important to ensure that the final dimensions meet the required tolerance range.
4) Guide Bushing
Typically, machining involves clamping the bar stock in a collet that slides into the spindle box behind the guide bushing. In the case of Swiss machining, the cutting tool operates close to the guide bushing, preventing any form of deflection.
Therefore, Swiss machines have a movable headstock and can maintain the required tolerances regardless of the workpiece length.
However, conventional CNC machining is different. The operator holds the workpiece in the spindle chuck. Therefore, this machining style is not suitable for longer workpieces as the workpiece can easily deflect.
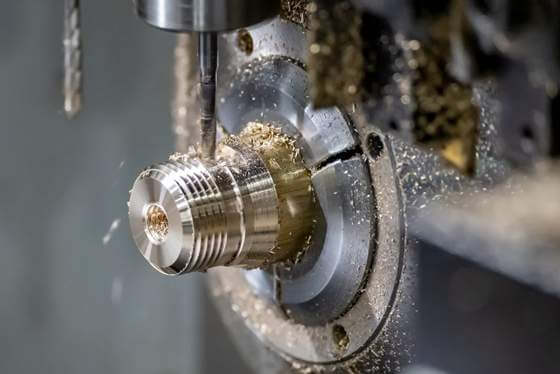
6.When should you choose Swiss CNC machining over conventional machining?
Swiss CNC machining is one of the most productive machining technologies for part machining. In addition to its short cycle time, it is suitable for machining the most complex Swiss machined parts.
Other reasons why you should consider CNC Swiss machining over conventional machining are mentioned below:
1) Complex Design
Swiss CNC machining is more suitable than conventional machining because it is suitable for complex designs. The process encourages the use of CAM (Computer Aided Manufacturing) software, making it suitable for machining complex parts. Therefore, product design is improved and errors are reduced due to reduced human involvement.
2) Setup Time
Swiss precision machining has special features such as onboard automatic setup probes and high damping composite castings (HDCC) that reduce the setup time of cutting tools.
3) Design for Manufacturing (DfM)
DfM is a part of part manufacturing that involves optimizing product design for ease of manufacturing and assembly. Introducing CNC into Swiss machining will make effective and efficient manufacturing processes much easier than traditional methods
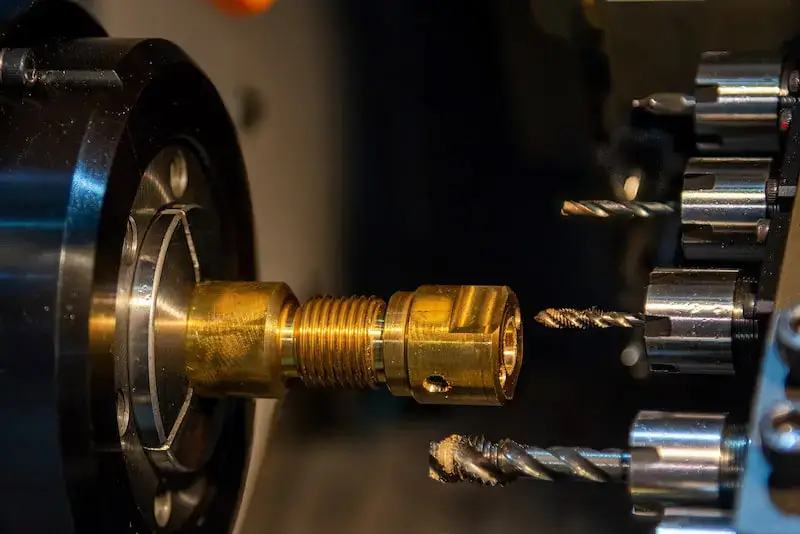
7.Practical Tips for Swiss CNC Machining
It is best to pay attention to several things when using Swiss CNC machining. For example, you must choose the right Swiss CNC machine and be able to operate the machine. However, the following tips will help you reduce costs and machining time.
Tip 1: Model Drawing
In order to achieve a precise machining process, the model drawing must be very accurate, clear, easy to read, and precise. In addition, it allows the CNC operator to understand and machine your parts.
A correct and accurate model drawing will help you improve the tolerances, dimensions, tolerances, and surface finish of your parts.
Tip 2: Standard Size Holes
Although Swiss machining technology is suitable for small and deep holes, you should make sure to use standard size holes. Using standard size holes will reduce machining difficulty and cost.
Tip 3: Avoid sharp corners
Drill bits are mainly rounded, making it difficult to machine sharp internal corners. Therefore, you need to avoid sharp corners in your design during Swiss milling.
For projects that require this, you can try EDM or follow the options provided to you by the part manufacturing service. In addition, you should ensure that the fillet radius is larger than the diameter of the drilling tool to prevent chatter and premature wear of the tool.
Tip 4: Tolerance
Tolerances in part manufacturing increase the cost and time of Swiss CNC machining. Therefore, you should only assign tight tolerances to the important parts of the part.
Tip 5: Wall Thickness
Too thin wall thickness can cause metals to chatter during machining and plastics to warp and soften during machining, and these defects can reduce the surface quality and accuracy of the part.
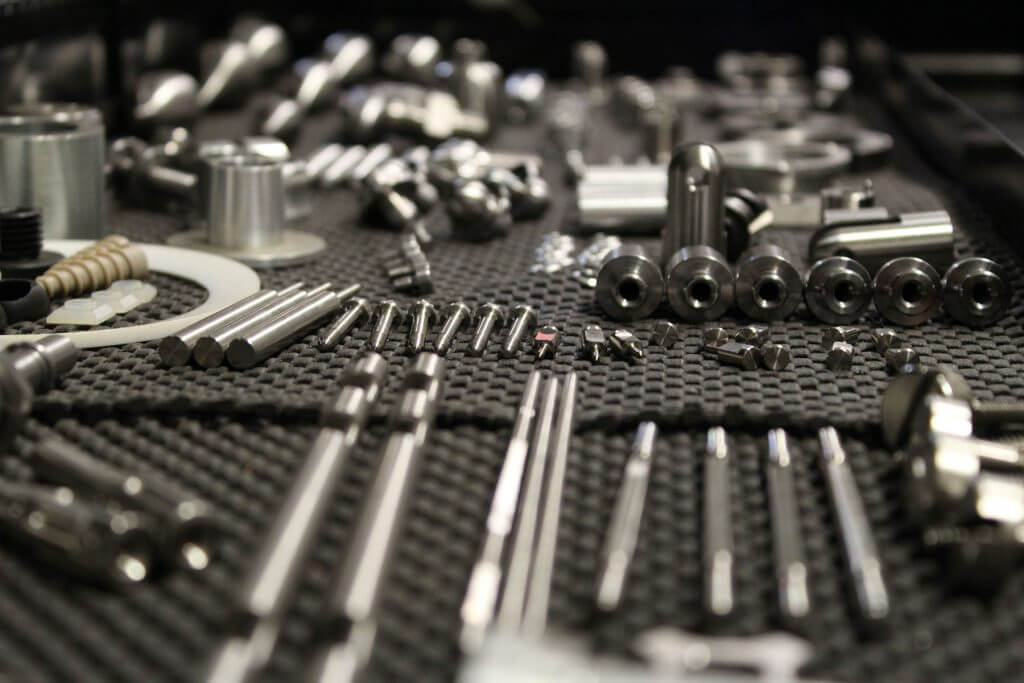
8.Applications of Swiss Machined Parts
Swiss machining is used in many industries to manufacture precision and small parts. For example, Swiss machined parts are components of strikers, medical devices, shafts, clocks, etc., as shown in the figure below.
1) Aerospace Industry
The process is suitable for manufacturing a variety of aerospace mechanical parts such as engines, wings, wheels, and cockpit controls. The process is an ideal machining process because it can achieve precision machining with tight tolerances.
2) Defense Industry
Swiss machines are highly accurate and suitable for producing geometrically complex components such as helicopters, missiles, ships, and tanks.
3) Consumer Electronics
Components used in consumer electronics require tight tolerances, high precision, high quality, smooth surfaces, and complex molding processes. Therefore, machines such as Swiss lathes are suitable for manufacturing components, lens housings, connectors, and joints.
In addition, it is also suitable for semiconductor-based devices such as electronic panels, controls, interfaces, printed circuit boards, and controls.
4) Medical Devices
Medical parts manufacturing is another industry that uses Swiss machine tools. Common medical Swiss machine tool parts include hinges, anchors, electrodes, and pull rings used in medical devices such as surgery, drug delivery, etc.
5) Automotive Industry
Swiss machines are suitable for manufacturing parts such as bushings, shafts, fuel injection components, pins, brake system components, etc. It is very popular among automotive parts manufacturers due to its high precision.
If you are looking for an experienced Swiss machining manufacturer, Xavier is your ideal choice. The Xavier team is well-equipped to provide high-quality CNC machining solutions. If you need more information or to discuss your machining needs with us, please feel free to contact us.