Introduction to vacuum casting
Vacuum casting is a soft mold technology that uses soft silicone molds to cast polyurethane plastics and elastomers. That’s where it gets its name, silicone casting and polyurethane casting. The entire casting process takes place within a vacuum chamber, eliminating the risk of air bubbles within the casting, making the final product precise and flawless.
Compared to traditional casting, where metal molds are permanent, costly and take long to produce, silicone molds are faster to make. Delivery time is approximately 15 days and one silicone mold can make up to 25 parts. This makes it the most preferred method for rapid prototyping.
Vacuum Casting Process: A Step-by-Step Guide
The key element of vacuum casting is the silicone mold. However, the making and use of silicone molds involves several pre-forming and post-forming steps. Here’s a quick rundown of all these steps:
Step 1: Create the master model
First, prepare a master mold to make the silicone mold. It enables 3D design on any CAD software such as SolidWorks, CATIA or AutoCAD. To make the mold lifelike, CNC machining or 3D printing are common options. The accuracy of vacuum cast parts depends largely on the master mold, so it needs to be as accurate as possible. For this purpose, the surface can be polished or ground.
Step 2: Make a silicone mold
After completing the master mold, proceed to casting the soft silicone mold. Place the master mold into the casting box and pour in the liquid silicone. For curing, place the device in an oven preheated to 40°C. Silicone may take 10 to 16 hours to set. Carefully remove the silicone mold with a knife. If release is difficult, use a release agent.
Step 3: Cast the part under vacuum
The final step is to pour the polyurethane into the silicone mold. If you are using mixed resins, mix them first. If you want any color, add colored paint now. Then, the air is pushed out of the mold to create a vacuum and the resin is poured in. This vacuum step is important because it stops bubbles from forming and ensures the resin covers every part of the mold.
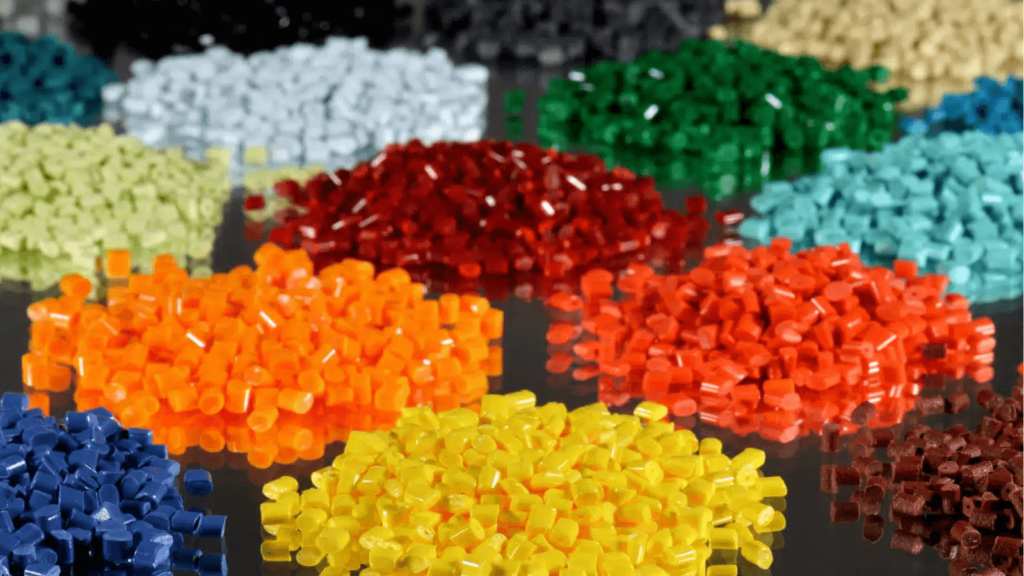
Materials used in vacuum casting
The silicone casting process is mainly suitable for polyurethane resins and elastomers. Some common material options are:
ABS-like resin
ABS resin has similar properties to ABS thermoplastic; it is hard, dimensionally stable and impact resistant. Among these resins, ABS-like UP4280 stands out for its heat resistance and high strength, making it a popular choice for prototyping. In addition, PX250 resin has high impact strength and UV resistance, qualities that are ideal for producing items such as helmets. For rapid prototyping, PX100 provides another viable option, ensuring there is an ABS-like resin available for a variety of applications. This structured approach highlights the specific benefits and applications of each ABS resin type, keeping the content logically consistent.
Glass filled nylon
Glass-filled nylon-like materials significantly improve the performance of vacuum cast products. By incorporating glass fibers into a nylon matrix, the material’s tensile strength and stiffness are significantly increased. This reinforcement allows it to withstand higher mechanical loads and stresses, making it ideal for applications requiring durability and resilience. Its unique composition ensures that components made from glass-filled nylon-like materials are not only stronger, but also better able to withstand rigorous use.
Elastomer-like TPE
Thermoplastic elastomers such as rubber are also ideal for molding. UP8400 is a rubber-like elastomer with black or white appearance, high fluidity and high elongation. It is used in the manufacture of gaskets, seals and handles. T0387 is an example of a translucent rubber-like material that is optimized for vacuum casting.
computer-like
It is a transparent, lightweight, high-strength material that is easy to process. Two PC-like materials, PX510 and UP6160, are commonly used in vacuum casting. They excel in applications requiring durability and visual clarity, are easy to machine, and are capable of producing precise, detailed parts. These materials are ideal for manufacturing parts where strength and aesthetics are critical, making them indispensable in the world of vacuum casting.
Transparent resin
Clear resins such as PMMA/acrylic are heat-resistant, shatterproof, and have medium strength. They are an excellent choice for casting clear castings and panels. X522HT is an example of a translucent plastic resin that can be used for silicone molding.
High impact resin
High-impact resins, such as UP5690, which is similar to polypropylene (PP), and PU8098, which is similar to polycarbonate (PC), are designed to replicate the desired properties of similar resins. These materials have excellent impact strength and chemical resistance, making them ideal for applications with high loads. The robustness and durability of UP5690 and PU8098 make them valuable for producing parts that require resilience and reliability under pressure.
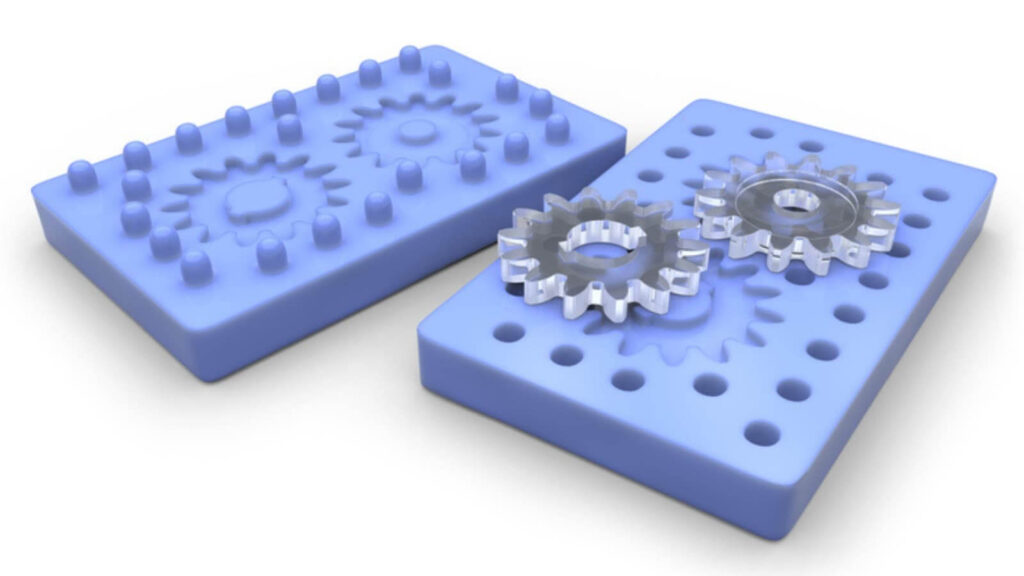
Vacuum Casting Design Guide
These guidelines will help you design accurate vacuum cast products and fine-tune details during the design phase.
tolerance
Designing with tolerances in mind ensures your components fit together and meet required specifications. In silicone mold casting, the shrinkage rate is 0.15%. Therefore, the design must follow this.
chamber wall thickness
With vacuum casting, you can freely incorporate different wall thicknesses into the same part. However, for best results it is best to maintain consistency and keep wall thickness to at least 1.5mm to ensure structural integrity.
rib cage
Adding ribs increases strength and reduces warping, especially in large flat areas. Its thickness needs to be less than the adjacent wall thickness to prevent shrinkage and sinking. Ideally, stiffener thickness should be less than 60% of the nominal wall thickness.
boss
Bosses are common when designing enclosures or housings. They increase the strength of attachment points. Their minimum diameter height should be 1 mm. Additionally, to minimize the risk of sinking, the wall thickness should not exceed 60% of the part’s nominal thickness.
undercut
Unlike processes that require hard tools, undercuts in vacuum casting do not require the use of inserts and can be designed freely.
Embossed details
For text and logos that are embossed (raised) or debossed (debossed), maintain a minimum depth or height of 1mm and a minimum width of 1mm to ensure these details are clearly visible. Additionally, a 1mm gap is maintained between characters to enhance readability.