Main advantages of CNC drilling machines
In today’s manufacturing industry, CNC drilling machines are leading the change and development of the industry with their excellent performance and significant advantages. CNC drilling machines, with their advanced computer numerical control (CNC) systems, bring unprecedented accuracy, efficiency and productivity gains to the manufacturing industry compared to traditional drilling methods. Next, let’s dive into the many benefits of CNC drilling machines in industrial applications.
1. high precision
In traditional manual drilling, the accuracy of the hole depends largely on the operator’s skills and experience, which inevitably leads to a certain degree of error. However, CNC drilling machines are completely different. They are pre-programmed to perform drilling operations accurately and control the error within a very small range. This accuracy is crucial for industries such as aerospace and automotive that require extremely high precision. Because in these fields, even the slightest deviation can cause serious consequences.
With CNC drilling machines, manufacturers can ensure that each hole strictly meets precise specifications. Whether it is the diameter, depth or position of the hole, a high degree of consistency and accuracy can be achieved, resulting in products of excellent quality and stable performance. This high-precision drilling capability not only meets the stringent requirements of high-end manufacturing for component accuracy, but also provides a solid guarantee for product quality and reliability.
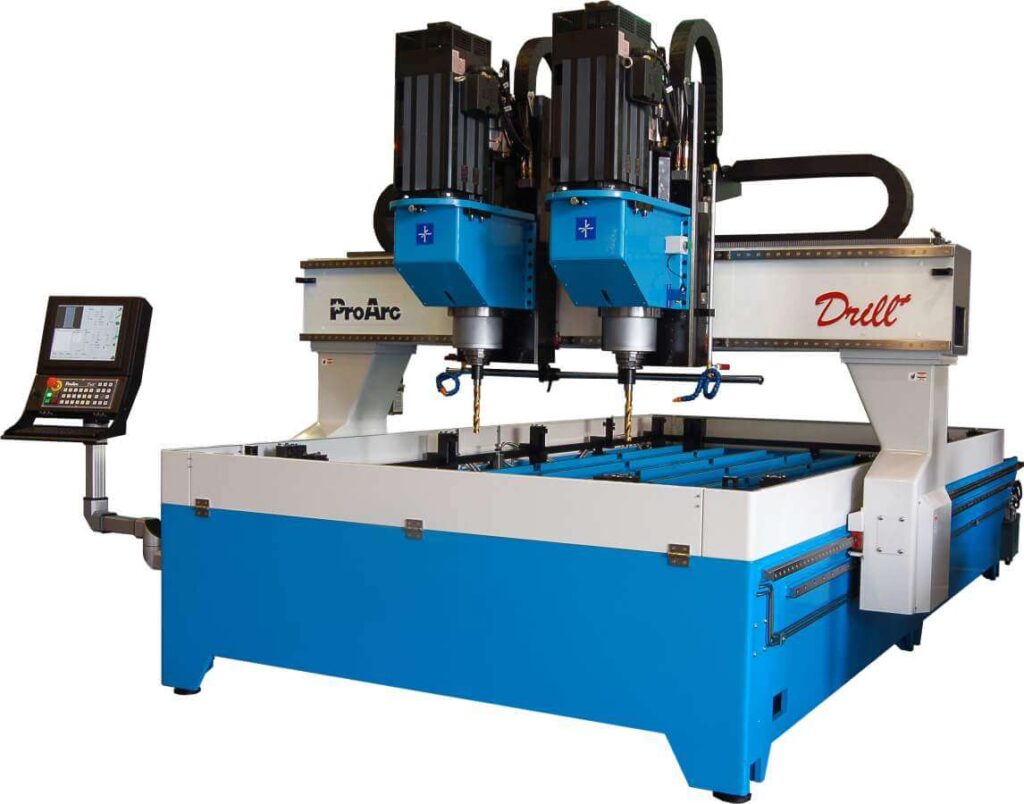
2.Improve efficiency
CNC drilling machines excel at increasing productivity. Unlike traditional single-pass drilling methods, these advanced machines have the ability to drill multiple holes simultaneously, which significantly reduces the time required for drilling operations. Additionally, they are able to easily execute complex drilling patterns and sequences without the need for tedious human intervention.
This automated drilling process not only greatly saves time, but also significantly reduces the risk of human error. Manufacturers can rely on CNC drilling machines to consistently produce high-quality products, effectively increasing overall productivity. Through efficient drilling operations, companies can respond to market demand faster, shorten product production cycles, and enhance market competitiveness.
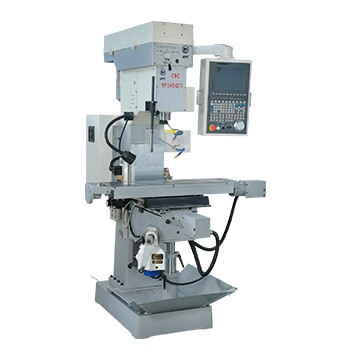
3.High safety
In manual drilling operations, operators face many potential dangers, such as flying debris that may cause damage to the eyes and body, the risk of accidental injury when the sharp drill bit rotates at high speed, and long-term repetitive operations may also cause the operator to suffer from occupational diseases such as repetitive strain. In contrast, CNC drilling machines provide operators with higher safety guarantees.
These machines can be operated at a safe distance, minimizing the risk of accidents. In addition, CNC drilling machines are also equipped with a series of safety features, such as emergency stop buttons, which can quickly stop the machine operation in emergencies to avoid further expansion of accidents; automatic tool changers reduce the potential dangers in the manual tool changing process. The existence of these safety features not only protects the life and health of operators, but also provides strong support for the safe production of enterprises.
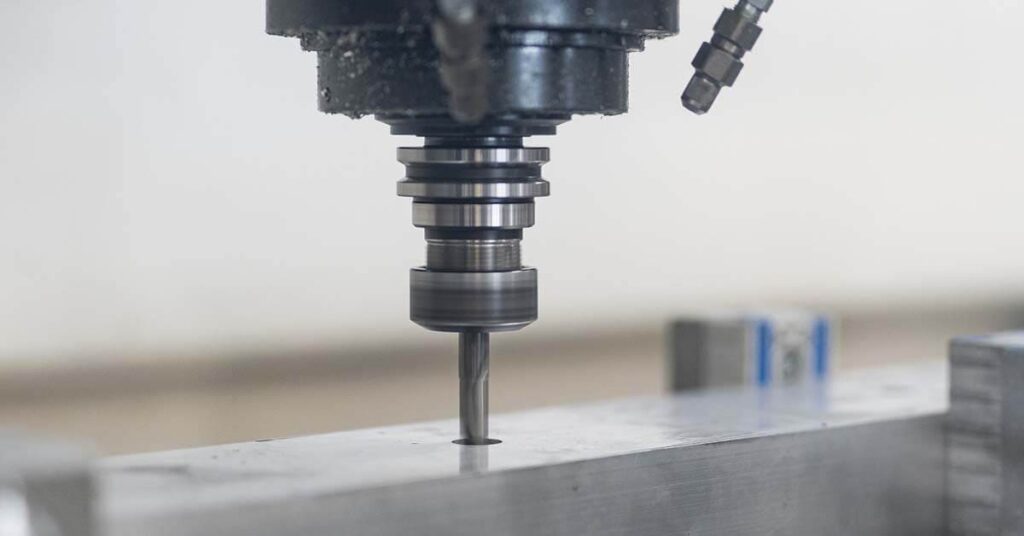
4.Conclusion
From a cost-effectiveness perspective, CNC drilling machines are a wise investment for manufacturers. Since CNC drilling machines require little maintenance, they last longer, reducing downtime and repair costs. In addition, the increased efficiency and productivity of CNC drilling machines can lead to higher output and profitability for manufacturers.