Introduction to CNC Surface Treatment Options
The two most common post-processing operations used in CNC machining manufacturing are heat treatment (annealing, case hardening) and surface treatment (shot peening, powder coating, etc.). Applying the correct surface treatment helps improve the surface roughness and the aesthetic and functional properties of CNC machined parts. The operations associated with surface treatment are as follows.
1.Sandblasting
The sandblasting process involves ejecting a pressurized stream of fine media beads (plastic or glass beads) from a nozzle onto the surface of the part. This removes burrs and imperfections and smoothes the surface. In addition, the final product has a uniform satin finish.
Sandblasting is performed in an enclosed chamber. Sandblasting with glass beads is more common on CNC machined parts. Since the surface is matte, it is ideal for preliminary surface treatment for painting and staining. Sandblasting is also an ideal surface treatment before anodizing to create a non-reflective surface.
The recommended part size is 6-600 mm in both height and width. Smaller parts are difficult to hold and it is difficult to produce a flat surface.
2.Electroless Nickel Plating
Electroless nickel plating or nickel phosphorus is the deposition of a uniform layer of nickel-phosphorus alloy on the upper surface of a solid substrate such as aluminum or steel. The substrate is immersed in an aqueous solution containing nickel salts and a phosphorus reducing agent. The process allows for a uniform coating of the substrate, unlike electroplating, which is affected by the uneven current density and resistance of the substrate.
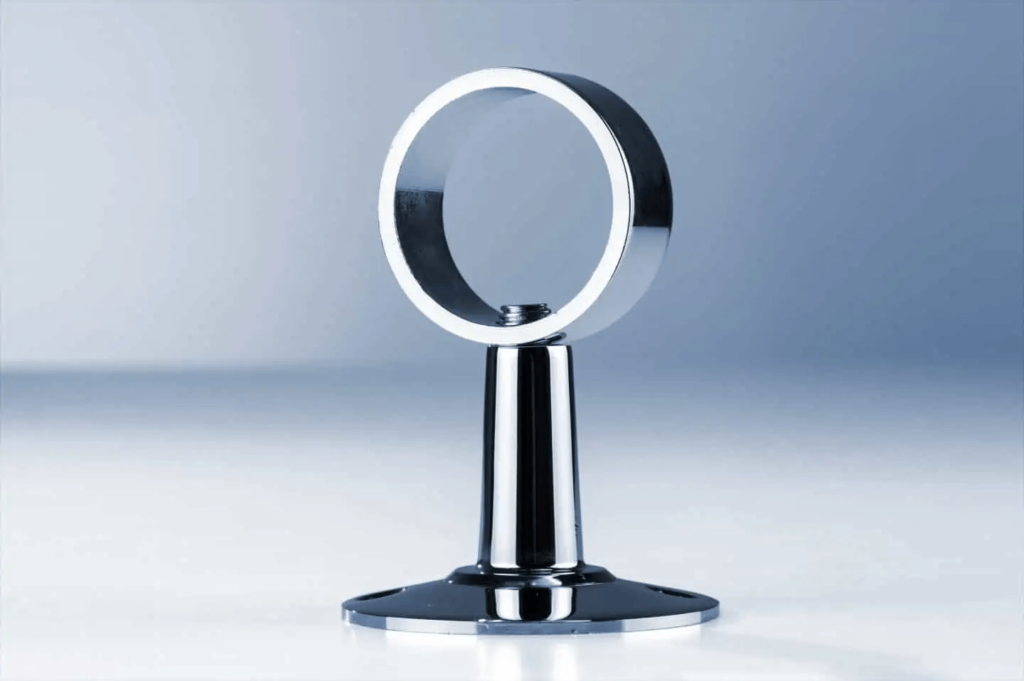
3.Powder Coating
The powder coating process involves applying a free-flowing dry powder to the substrate. Unlike normal liquid coatings that use evaporating solvents, powder coatings are applied electrostatically and cured under heat or UV light. The powder can be either a thermoplastic or thermosetting polymer. The coating is generally stronger and more uniform than conventional coatings. Metals such as aluminum and steel can be effectively coated with polymer powders.
4.Electrolytic Polishing
Electrolytic polishing is the exact opposite of electroplating. In electroplating, the substrate is the cathode and the sacrificial anode transfers its ions to the cathode. Here, the situation is reversed and the substrate is the anode and its ions move toward the cathode. In the process, tiny peaks and valleys are smoothed out. This is a very good technique for removing burrs and reducing the average surface roughness.
5.Passivation
Passivation is a process that primarily involves stainless steel, which is primarily composed of iron, chromium, and nickel. The corrosion resistance of stainless steel is provided by the chromium in the alloy, as it naturally produces a layer of chromium oxide on the surface, while free iron promotes corrosion.
Passivation involves immersing the stainless steel in an acidic bath (such as nitric acid), which dissolves the free iron and increases the strength of the chromium oxide, thereby resisting corrosion.
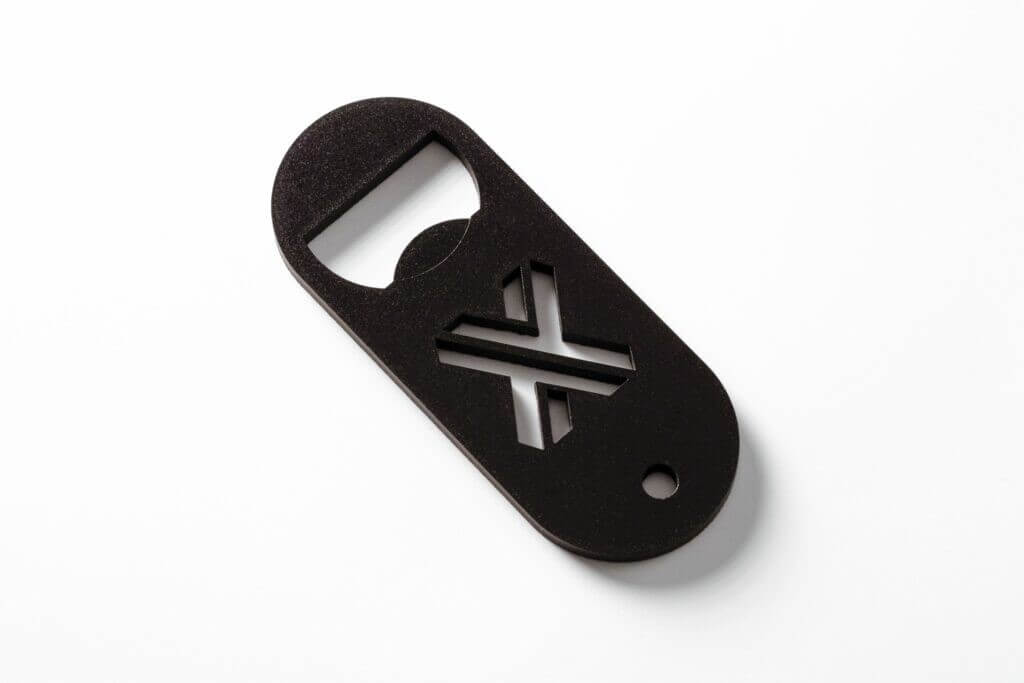
6.Anodizing
Anodizing is similar to passivation in that it increases the thickness of the oxide layer, which makes the metal surface corrosion-resistant. It is very common for aluminum in CNC machining. It is different from passivation, which involves more than just immersion in acid, but also involves an electrolytic process. Therefore it is also called electrolytic passivation.
During the anodizing process, the aluminum alloy is immersed in a sulfuric acid electrolyte and used as an anode. When a cathode (an inert material such as stainless steel, nickel, carbon, etc.) is placed and electricity is applied, oxygen flows to the anode and reacts to form an anodic oxide. This anodic oxide contains primarily aluminum oxide, which prevents corrosion.
The electrolyte is typically:
- A 10–15% sulfuric acid solution at 25°C, producing about 25µm of oxide layer per hour
- A mixture of oxalic and sulfuric acid at 30°C, producing about 30µm per hour
- 10% chromic acid running at 38–42°C, producing about 15µm/hour
Anodizing also produces a rough and grainy effect on the metal surface. It also traps dyes in the oxide layer, producing a nearly permanent color.
7.Galvanizing/Galvanizing
Galvanizing is primarily associated with steel. Galvanizing, also known as hot-dip galvanizing, is the process of coating steel with multiple layers of zinc-iron alloy and zinc metal by immersing it in a bath of molten zinc. This is because the zinc chemically reacts with the iron content in the steel and diffuses the coating perpendicular to the surface, forming a uniform, thick layer along the surface.
If you are looking for an experienced surface treatment manufacturer, Xavier is your ideal choice. The Xavier team is well equipped to provide high-quality surface treatment solutions. If you need more information or want to discuss your processing needs with us, please feel free to contact us.