Zinc Processing: Different Alloys and Processes for Making Zinc Parts
Zinc processing is a crucial step in the manufacturing of various products, as it allows for the creation of durable and corrosion-resistant zinc parts. In this article, we will provide an overview of the different alloys and processes used in zinc processing, highlighting their importance and applications.
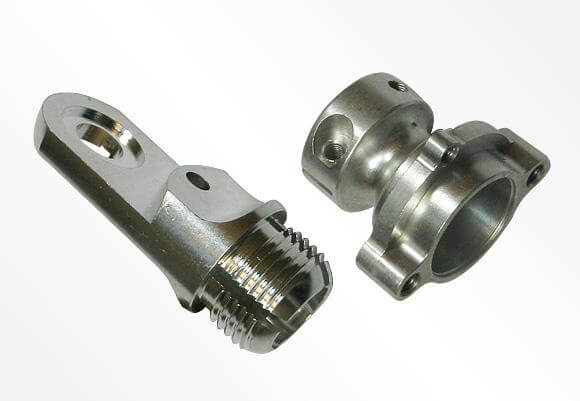
1.Different alloys
1) Brass
One of the most commonly used alloys in zinc processing is brass, which is a combination of zinc and copper. Brass is known for its excellent strength and malleability, making it ideal for applications such as plumbing fittings, musical instruments, and decorative items. The addition of copper to zinc enhances its corrosion resistance and gives it a distinctive golden color.
2) Bronze
Another popular alloy used in zinc processing is bronze, which is a mixture of zinc and tin. Bronze is highly valued for its durability and resistance to wear and tear, making it suitable for applications such as statues, bearings, and electrical connectors. The addition of tin to zinc improves its strength and hardness, making it an excellent choice for applications that require high performance.
3) Others
In addition to brass and bronze, zinc can be alloyed with other metals such as aluminum, magnesium and nickel to form specialized alloys with unique properties. For example, zinc-aluminum alloy, also known as zinc-aluminum or galvalume, is widely used in the construction industry as a roofing and cladding material. At the same time, these alloys also offer excellent corrosion resistance and are lightweight, making them ideal for construction applications.
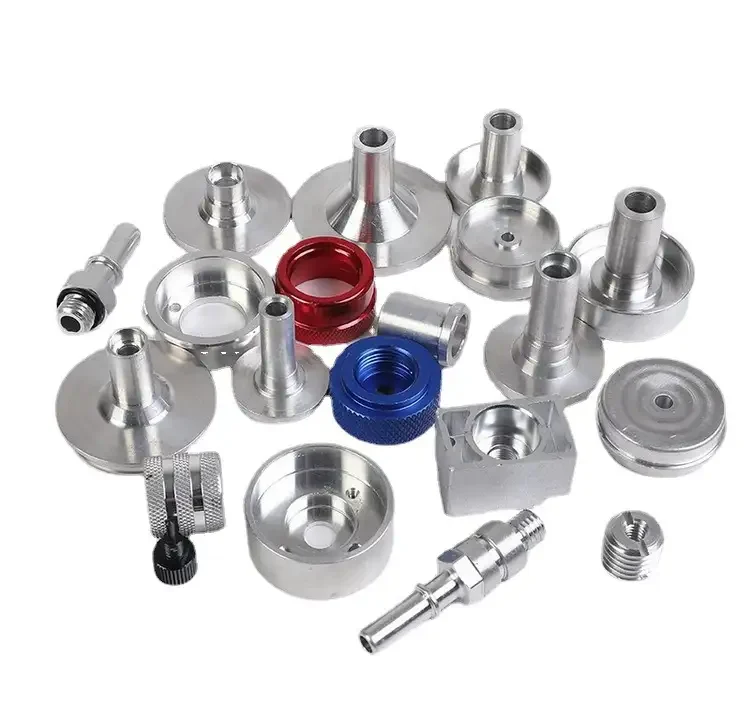
2.Various processes for zinc processing
Now that we have discussed the different alloys used in zinc processing, let’s delve into the various processes involved in creating zinc parts.
1) Die casting
One of the most common processes is die casting, which involves injecting molten zinc into a mold cavity under high pressure. This process allows for the production of complex shapes with high precision and efficiency. Die casting is widely used in industries such as automotive, aerospace, and electronics.
2) Galvanizing
Another important process in zinc processing is galvanizing, which involves coating steel or iron with a layer of zinc to protect it from corrosion. Galvanizing is achieved through a hot-dip process, where the steel or iron is immersed in a bath of molten zinc. This process creates a metallurgical bond between the zinc and the substrate, providing long-lasting protection against rust and corrosion. Galvanized steel is commonly used in construction, automotive, and agricultural applications.
3) Electroplating
Electroplating is another process used in zinc processing, where a thin layer of zinc is deposited onto a metal surface through an electrochemical reaction. This process is commonly used to enhance the appearance of metal objects and provide them with corrosion resistance. Electroplating is widely used in the manufacturing of jewelry, automotive parts, and household appliances.
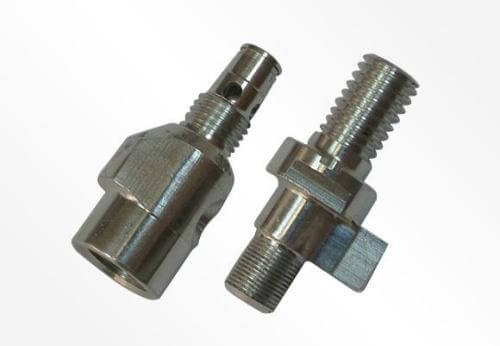
In conclusion, zinc processing plays a vital role in the manufacturing industry, allowing for the creation of durable and corrosion-resistant zinc parts. Different alloys such as brass, bronze, and zinc-aluminum offer unique properties and applications. Processes such as die casting, galvanizing, and electroplating enable the production of high-quality zinc parts for various industries. Understanding the different alloys and processes involved in zinc processing is essential for manufacturers looking to create reliable and long-lasting products.