Zinc vs Aluminum Die Casting: The Best Guide
Die casting is an advanced manufacturing technology suitable for producing parts with complex designs, high precision requirements and large quantities. Among the many metals used for die casting, zinc and aluminum are the most popular choices due to their unique performance advantages.
In this blog, we will compare the properties of zinc and aluminum in depth, their respective advantages and disadvantages, etc., aiming to provide you with professional reference when making a choice.
1.Characteristics of zinc alloy
Composition: It is composed of zinc and other elements such as aluminum, copper, magnesium or tin.
Melting point: about 420℃, which is suitable for hot chamber die casting process.
Density: about 5g/cm³, heavier and stronger than most die casting materials.
Performance: It has excellent thermal conductivity, can cast complex, thin-walled, precision parts, has a smooth surface, high dimensional accuracy, and can accept various surface treatments.
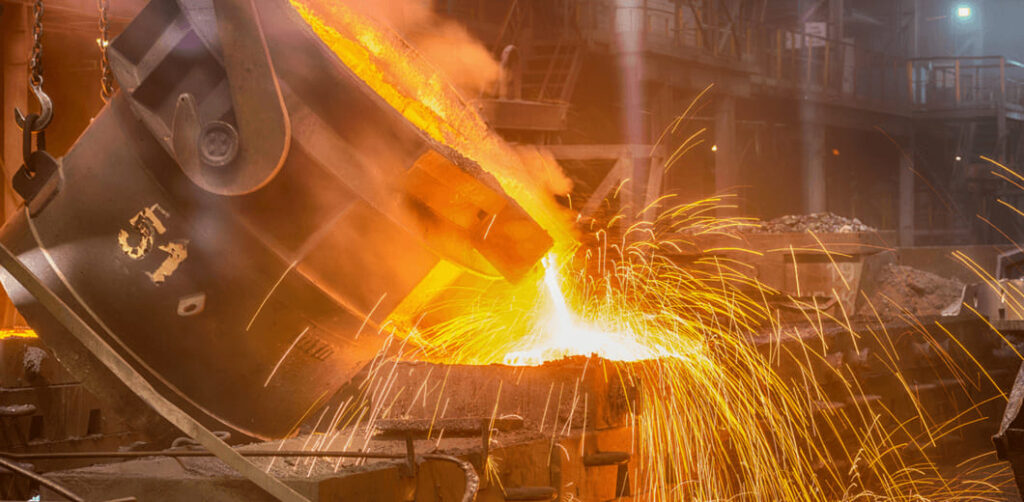
2.Characteristics of aluminum alloy
Composition: It is composed of aluminum and other elements such as silicon, copper, magnesium or zinc.
Melting point: about 660℃, which is suitable for cold chamber die casting process.
Density: about 2.7g/cm³, lighter and corrosion-resistant.
Performance: It has excellent electrical and thermal conductivity, can cast parts with good mechanical properties, and is easy to process after casting.
3、The Difference Between Zinc and Aluminum Die Casting
1.Weight
Zinc castings are heavier than aluminum castings and have a higher density. Heavy parts provide stability and impact resistance for structural applications, and light parts reduce fuel consumption and improve performance in automotive applications.
2.Strength
Zinc castings are stronger, have high density and low porosity, can withstand higher loads and pressures, but are more susceptible to aging due to low thermal stability.
3.Durability
Aluminum die castings are more durable, have low density and high corrosion resistance, and are better at resisting oxidation and rust in humid or salty environments, but are more susceptible to fatigue.
4.Surface quality
Zinc die castings have a low melting point, high fluidity, better surface quality, easy mold filling, smoother surfaces and finer details, but are more sensitive to temperature changes.
5.Cost
Zinc die castings are cheaper, have a low melting point and high compatibility with hot chamber processes, and reduce production costs, but the material cost is more expensive due to its high density.
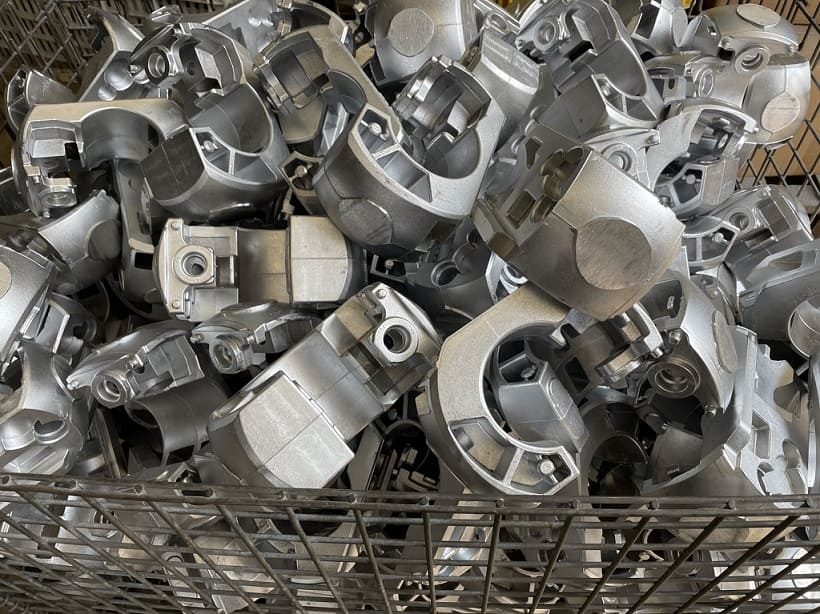
4、Situation of choosing zinc die casting
1.Thin-walled parts
The high fluidity and low injection pressure of zinc can produce thin-walled parts, saving weight and material costs.
2.Harsh environmental conditions
Zinc die-cast parts have high corrosion resistance and durability, and can withstand harsh environments such as humidity, salt spray or chemicals.
3.Small residual stress
Zinc is suitable for manufacturing parts with complex shapes and fine details. It has good fluidity, low pressure, and little damage to the mold, saving mold maintenance costs.
4.Faster production
Zinc has a low melting point and a fast solidification speed. It can be used with hot chamber technology to produce fast, reducing cycle time and production costs.
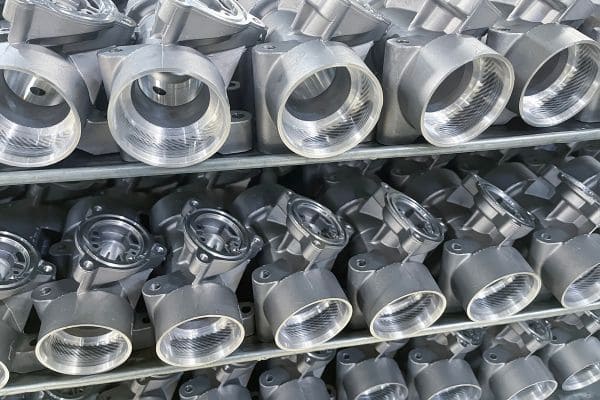
5、Situation of choosing aluminum die casting
1.High strength-to-weight ratio
Aluminum castings have low density and high tensile strength, which can produce parts with a high strength-to-weight ratio, reducing weight and material costs.
2.High operating temperature
Aluminum castings have high thermal conductivity and low thermal expansion, can withstand high operating temperatures, and have good heat resistance and stability.
3.Electrical conductivity
High aluminum content can produce highly conductive parts, improving electrical efficiency and functionality.
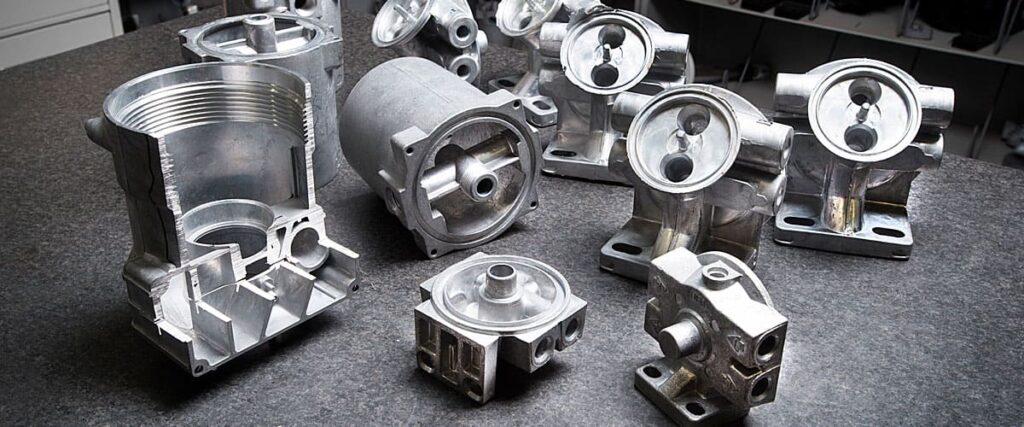
Conclusion
Zinc and aluminum die casting are versatile and cost-effective methods of producing high-quality metal parts, but they have different properties and applications. When choosing one for your project, you should make an informed decision based on the characteristics of the respective parts.
If you are looking for an experienced processor, Xavier is your best choice. The Xavier team is well-equipped and skilled in all types of die casting to fully meet your processing needs. If you need more information or to discuss your processing needs with us, please feel free to contact us.